Key Technology
關鍵技術
Gasification, popular? Incinertor, out of fashion? An Analysis on the Waste Treatment Factory Pros and Cons
The efficiency of energy recycle has become a significant benchmark for future waste treatment. This article makes an attempt to explore and analyze new technologies that are rapidly developing around the world in recent years, focusing on the incineration and gasification technologies.
The Pollution Control of Incineration Improved
Incineration is now a highly mature technology with over 1,300 projects (HPCC grate type) around the world. In the past, one of the biggest concerns associated with incineration was the issue of air pollution, especially the emission of dioxin. In recent years, incinerator manufacturers continued to improve the technology of combustion control and have greatly reduced the dioxin and nitrogen oxides produced during the incineration process. According to the technical statistics released by several suppliers of large-scale incinerators currently in the market, advanced combustion control system is capable of capping the concentration of dioxin emission below 2ng-TEQ/Nm3 measured at boiler outlet, which is more than 50% reduction over the previous technology. For nitrogen oxide, the advanced combustion control technology, aided by advance SNCR, has achieved effective control on the concentration of nitrogen oxides at 70 to 80 ppm and below, which is approximately 20% reduction in emissions compared with the capability of current mainstream technology in Taiwan (Figure 1).
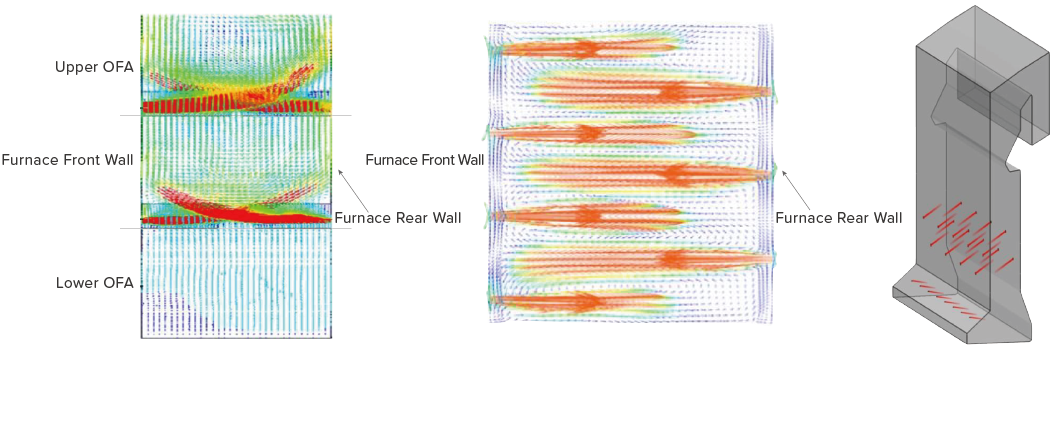
Figure 1. Advance combustion modeling was used to design the air system, to ensure combustion efficiency and minimum formation pollution.
Energy Efficiency of Incinerator Improved Greatly
One of the main causes of low energy efficiency at waste incineration plants is excessive air supply. To ensure thorough combustion of the waste, an incineration plant often supplies excess air ratio about 1.8~2.0, which more than supplied at a coal power plant (excess air ratio about 1.2). Nowadays, new and advanced combustion control and water-cooling of grate technology reduced the need for air supply. The new incinerators require only 1.4 to 1.5 times of excess air supply during incineration. Lower excess air supply means less flue gas emission, less burden on the air-pollution control facilities and less energy consumption, while improving boiler efficiency and increasing steam production. However, regulations in Taiwan concerning emission of dioxin require the flue gas output measured at boiler outlet to have no less than 6%(wet base) of oxygen content. In such case, supply of excess air ratio can only be reduced to around 1.6 and this result in effect limits continuous improvement on boiler efficiency. If we want to reduce the oxygen content of the flue gas(<6%), a separate verification document shall be submitted to government for application. In the past, incineration plants generally controlled the waste gas temperature at boiler outlet in a range between 220℃ and 260℃ to prevent corrosion on the pipes of the economizer. Now, in new incineration plants, the operating temperature is controlled in the range between 180℃ and 200℃ through replacing the old-style pipes for the economizer with pipes constructed with anti-corrosion materials. Through the above technologies, boiler efficiency can be substantially increased from 78% to 85% or higher with a new-style incineration plant.
EfWs Efficiency Steadily Increased
For increase the power generation, there are two common directions as following: (1)Increase steam temperature and pressure The higher the steam temperature and pressure, the higher the electricity recovery at the turbine generator will be. However, the new incineration technology often controls the temperature between 420℃ to 440℃, due to the fact that high steam temperature substantially expedites heat corrosion on the boiler pipes. Some manufacturers integrate other power generation facilities to utilize the residual heat of the flue gas and increase the temperature of superheated steam up to 500℃. This technology not only improves the efficiency of power generation, but also successfully prevents high temperature corrosion. (2)Reduce the steam temperature and dryness at turbine outlet. Currently, the most commonly-used technology can increase the degree of vacuum down to -0.85kg/cm2G. (3)Steam reheating technology. This technology is often used in large-scale power plants. Leftover steam captured after first round of turbine generator is reheated and guided into the second section of turbines for power generation. Fourth generation incineration plants in the Netherlands now use this technology, which effectively increased the efficiency of power generation for over 30%.
Gasification Converted the Organic Matter into Syngas
In theory, gasification technology promotes reaction between organic matter and steam under limited supply of oxygen and high temperature to convert the organic matter into syngas (carbon monoxide, hydrogen and methane). One of the advantages of gasification technology is the ability to produce a syngas that has higher efficiency than the original fuel. After purification, syngas can be used for power generation or reprocessed to become a synthetic fuel. The purification process removes the acidic gas and tar that cause corrosion and blockage of the facilities, making it highly suitable for use with high efficiency electricity recovery systems, such as gas boiler or gas turbine.
Less Dioxin Emission from Gasification
Furthermore, gasification technology breaks up dioxin under high temperature and treats syngas through sudden cooling and acid removal processes, which eliminates the dioxin emission problem in further utilization of syngas. Research literature pointed out that, under the same dioxin treatment technology, gasification facilities emits lower dioxin concentration (0.002 to 0.01ng-TEQ/Nm3) than incineration facilities. Since gasification reaction involves over 100 complex oxidation and reduction reactions, to ensure the quantity and quality of syngas production, there are strict standards to the operating temperature, air supply and waste quality (see Figure 2 & Figure 3) Therefore, to be processed under gasification technology, the requirements are relatively high in terms of the stability of the waste to be processed in the gasifier. The waste must be shredded, sorted and dried before they can be fed into the gasifier. In addition, the byproducts of gasification, eg. tar, is known to add substantial burden to the rear-end air pollution control system and gas turbine generator. Especially tar, the complexity of this substance adds cost to the rear-end process of syngas purification.
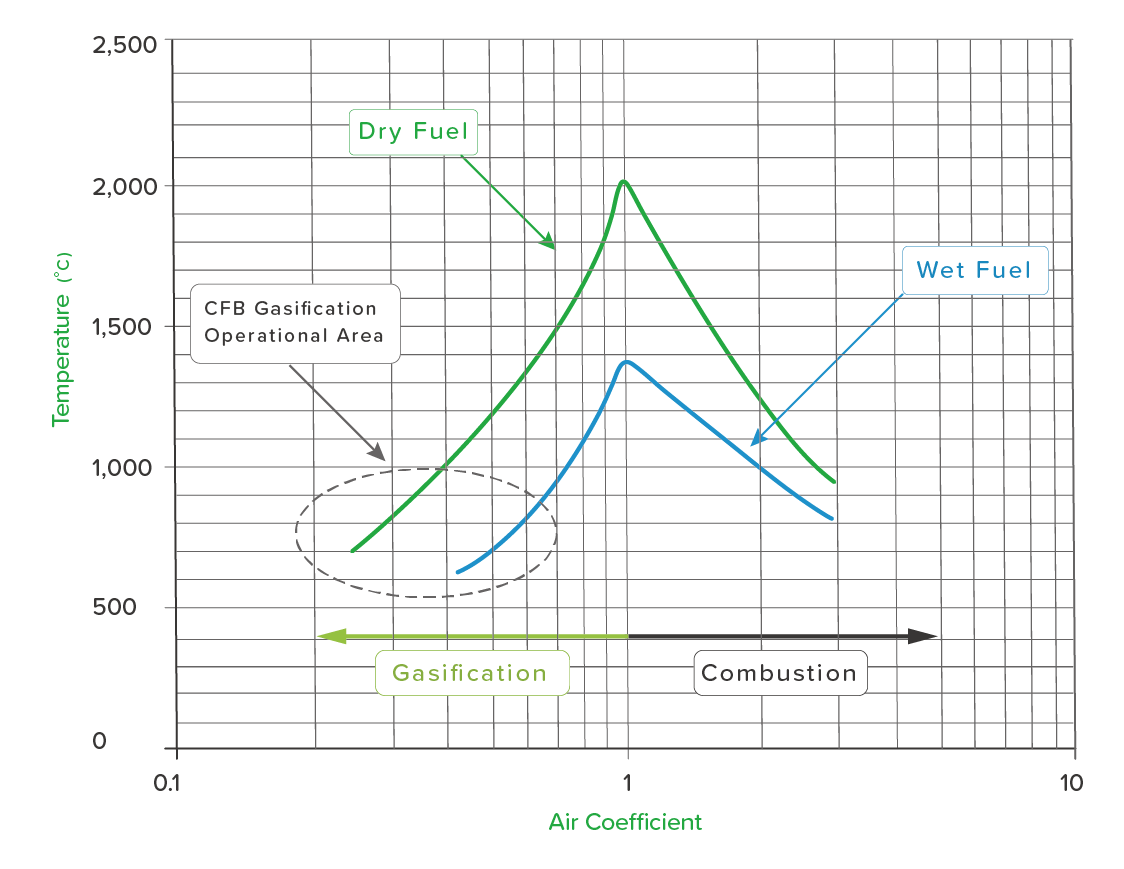
Figure 2. The effect of air supply volume to reaction temperature. The higher the air supply, the higher the gasification operating temperature. When the air coefficient is exceeds 1, it will become incinerated, and the gasification operation must be very cautious.
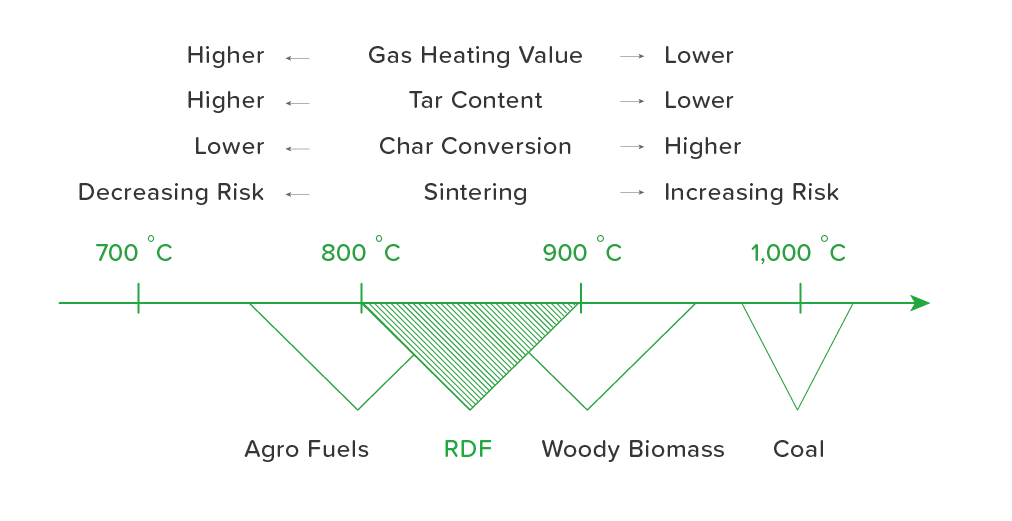
Figure 3. The effect of reaction temperature and the gasification products. The higher reaction temperature, the tar and char content can be reduced, but the heat value of syngas will be reduced at the same time.
Few Successful Cases of Waste Gasification Plants
Applications of gasification technology currently available in the market can be divided into two categories by reaction temperature: “gasification melting” and “gasification burning”. Currently, the majority of gasification melting plants, nearly 100 plants, are located in Japan with maximum processing capacity of 265 tons per day per gasifier. However, limited by the high cost and high temperature operation, the malfunction rate is higher than the incinerator plants, causing the annual operating rate to drop lower than 80%, and therefore growth in the number of new gasification facilities slowed down. For gasification burning technology, several projects are ongoing in Europe and the US, but there is only one large-scale facility (processing capacity >300 tons per day per gasifier) currently in operation, which operates with a capacity of 400 tons per day per gasifier with overall power generation efficiency as high as 30%. However, according to the statistics of 2015, this plant operated less than 7,000 hours per year. This shows that there is still room for improvement, especially for the syngas purification facilities. In addition, the mainstream gasifier used in Europe is the circular fluid-bed type, which producing more ash than the incineration technology by 2 to 3 times.
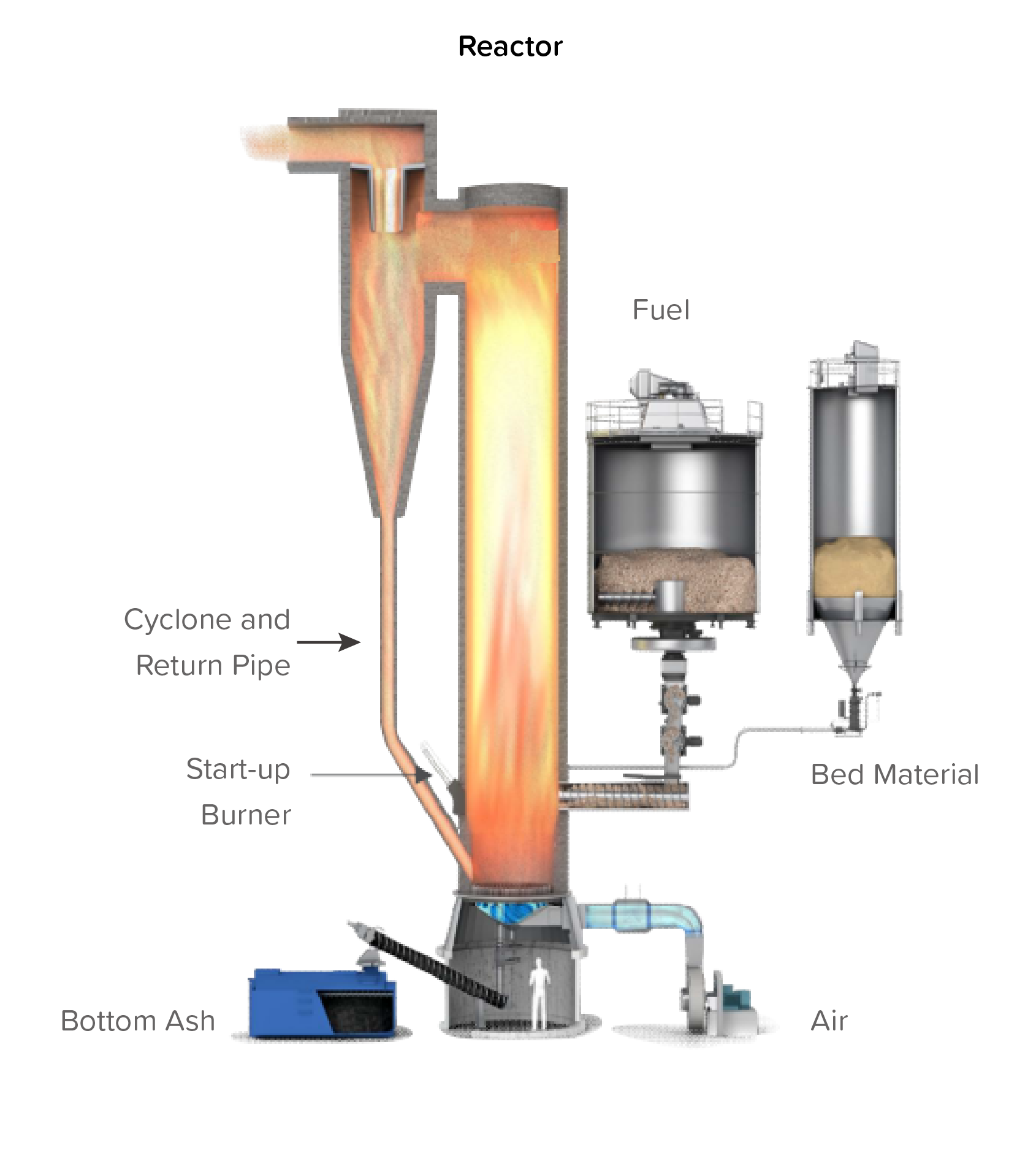
Figure 4 . The largest gasifier schematic in Europe. The mainstream gasifier used in Europe is the circular fluid-bed type, which producing more ash than the incineration technology by 2 to 3 times.
In Conclusion: Try to Set a Gasification Pilot Project at Outlying Islands
Through a long process of development and improvement, incineration technology has substantially increased the efficiency of energy recycle and, at the same time, reduces pollution. Thanks to Its higher tolerance to the volatility of waste while having the capability to treat the different types of waste (MSW, sludge, liquid, etc.), many countries give incineration the priority when choosing a system for waste treatment since it is more technologically matured. Gasification technology, on the other hand, has higher efficiency in terms of power generation. However, it is less tolerant to the volatility of waste, which means that the different types of waste must be treated to meet the strict standards before they can be fed for processing. Therefore, energy consumption at the pre-treatment stage must be reassessed. Gasification is also not suitable for waste with high moisture content (high moisture content means low heat value when converted into syngas and therefore lower fuel efficiency). Since gasification technology requires high homogeneity in the quality of the waste, it is not suitable for simultaneous processing of mixed waste, unlike incineration facilities. Therefore, most waste gasification plants overseas are relatively small in scale or generate electricity with added biofuels. In recent years, gasification technology has been actively promoted in the developed nations. In our national policies, pilot projects at the outlying islands have also been planned in the Multi-approach Waste Management Plan. We anticipate further development of this technology to be used for waste treatment in the near future.