Innovation
企業創新
ECOVE Optimizes Concentration & Purification Processes to Bring Waste Solvents Back to Supply Chain
ECOVE learned that some of the used waste solvents can be used as industrial products for secondary usage after the concentration and the purification processes with "distillation separation" and "extractive distillation" though they contain few impurities. Apart from acquisition cost reduction of raw materials, cost reduction of waste disposal as well as longer life cycle of solvents, such technologies and services maximize the most effective recycling of earth resources while implementing the circular economy philosophy of ECOVE.
Dispose Waste Solvents with the Distillation Separation
If the surplus of industrial waste solvents failed to be disposed in a proper way, poisoning could happen through skin absorption and inhaling. Besides, these substances could generate irritating or toxic gas after burning. Treatment plants used to dispose the waste physically or incinerate them as a kind of auxiliary fuel. At ECOVE, “Every Resource Counts” is the inherent spirit throughout the daily operation. We believe that it is wasteful if the industrial solvents are used as disposable materials. Instead, we shall treat them as renewable resources and find a most effective method to promote the waste solvent recycling by referencing international trends and the latest concentration and azeotrope technologies. First of all, ECOVE adopts the so-called "concentration technology" to finish the concentration or separation of effluents with low concentration and blended solvents. Common concentration technologies include thin film, extraction and distillation. According to our analysis and comparison, ECOVE found that the "distillation separation" is "extensively used" technology among companies that has many advantages. For example, it "does not run with the assistance of chemicals", which is of "large treatment capacity" and "continuous operation". Therefore, distillation separation is chosen to convert the waste solvents into marketable products.
Concentrate Matters with the Break-the-Azeotrope Technology
Generally, azeotropic mixture is always formed from hydrous organic solvents and easily cause the azeotropism during the concentration process. When it happens, the concentration of solvent will maintains in the azeotropic point instead of rising. To increase the concentration of waste solvents from recycling and reusing, ECOVE furthers the purpose of concentration process based on all pervading break-the-azeotrope technologies among companies, such as vacuum distillation, azeotropic distillation and extractive distillation. For the advantages and disadvantages of abovementioned technologies, please refer to Figure1 below. Upon analysis and comparison, we decided to use the extractive distillation as the break-the-azeotrope technology since it features the strong concentration effect and produces the recoverable extractants. Furthermore, moisture content of isopropanol after the concentration is taken into consideration. By assessment, pervaporation membranes free from any other chemicals are chosen for the dehydration in order to improve the isopropanol quality.
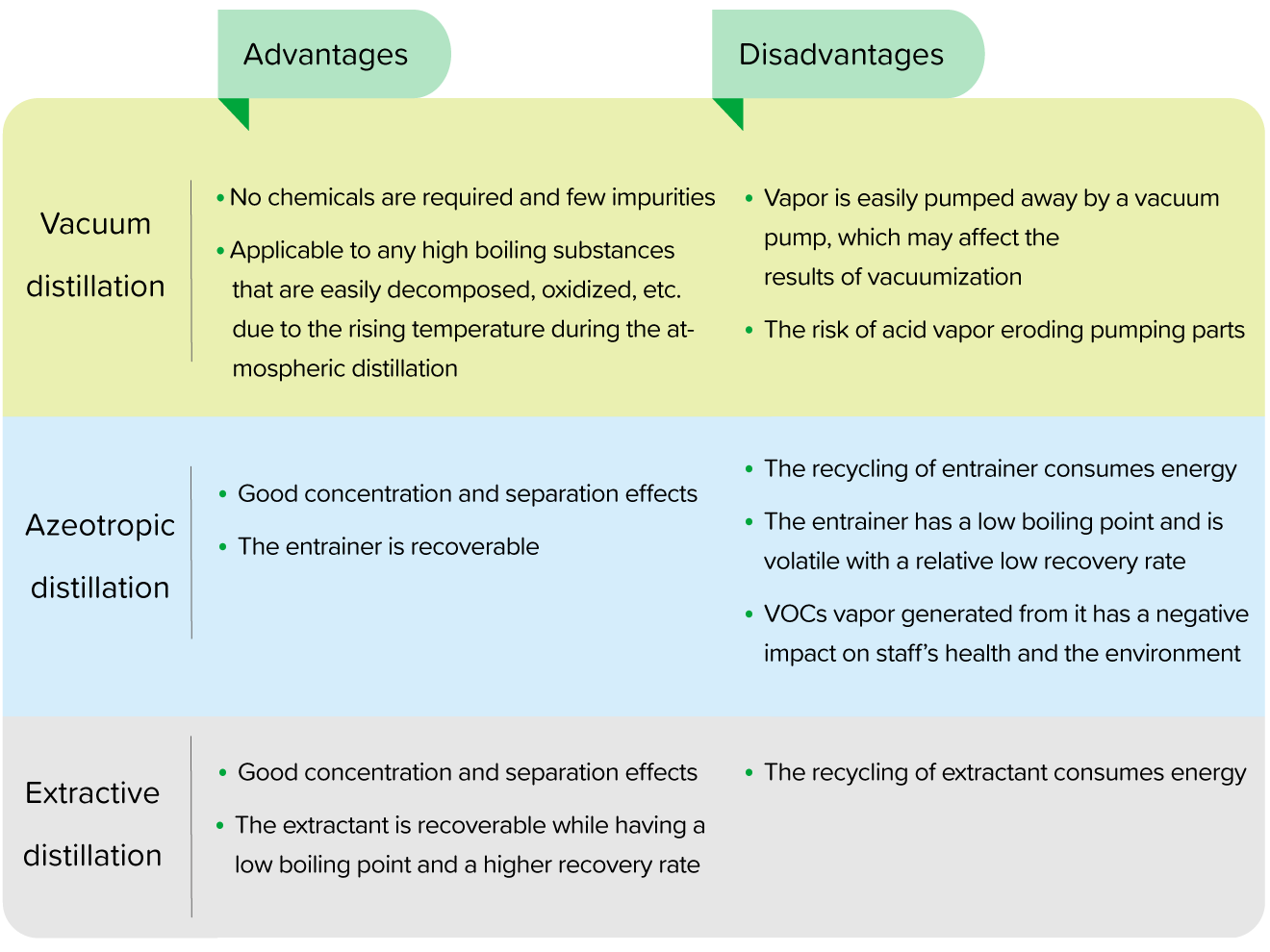
Figure 1. Advantages and disadvantages of the break-the-azeotrope technology related to waste solvents
Recycling & Reusing Waste Effluents to Achieve Sustainable Environment
ECOVE is expected to provide recycling and reusing service of waste solvents in the second half of 2019. The distillation separation is used for the front-end process so as to condense the waste isopropanol with low concentration into the industrial isopropanol product with 85% of concentration. The products can be used as industrial solvents for decontaminating, formulating chemical raw materials or for diluting and homogenizing coatings; as for the back-end process, the break-the-azeotropic distillation of extractive distillation is combined with the pervaporation membranes. It can condense the industrial isopropanol with roughly 85% of concentration into products with 99.5% of concentration depending on market demands and deliver the waste back to the production end. The upcoming service is conducive to acquisition cost reduction of raw materials, cost reduction of waste disposal as well as extending life cycle of solvents for companies, promoting the most effective utilization of resources. Besides, another favorable purpose that ECOVE runs the waste solvent recycling is: ECOVE has been engaged in incineration plant operation and waste disposal process over 20 years, forming the skilled, correct and proper treatment flow for waste solvents. Meanwhile, with the extensive experience in the operation and reformation of incineration plants, ECOVE can assess and optimize the equipment and systems of distillation separation for greatly improving the resource recycling efficiency.
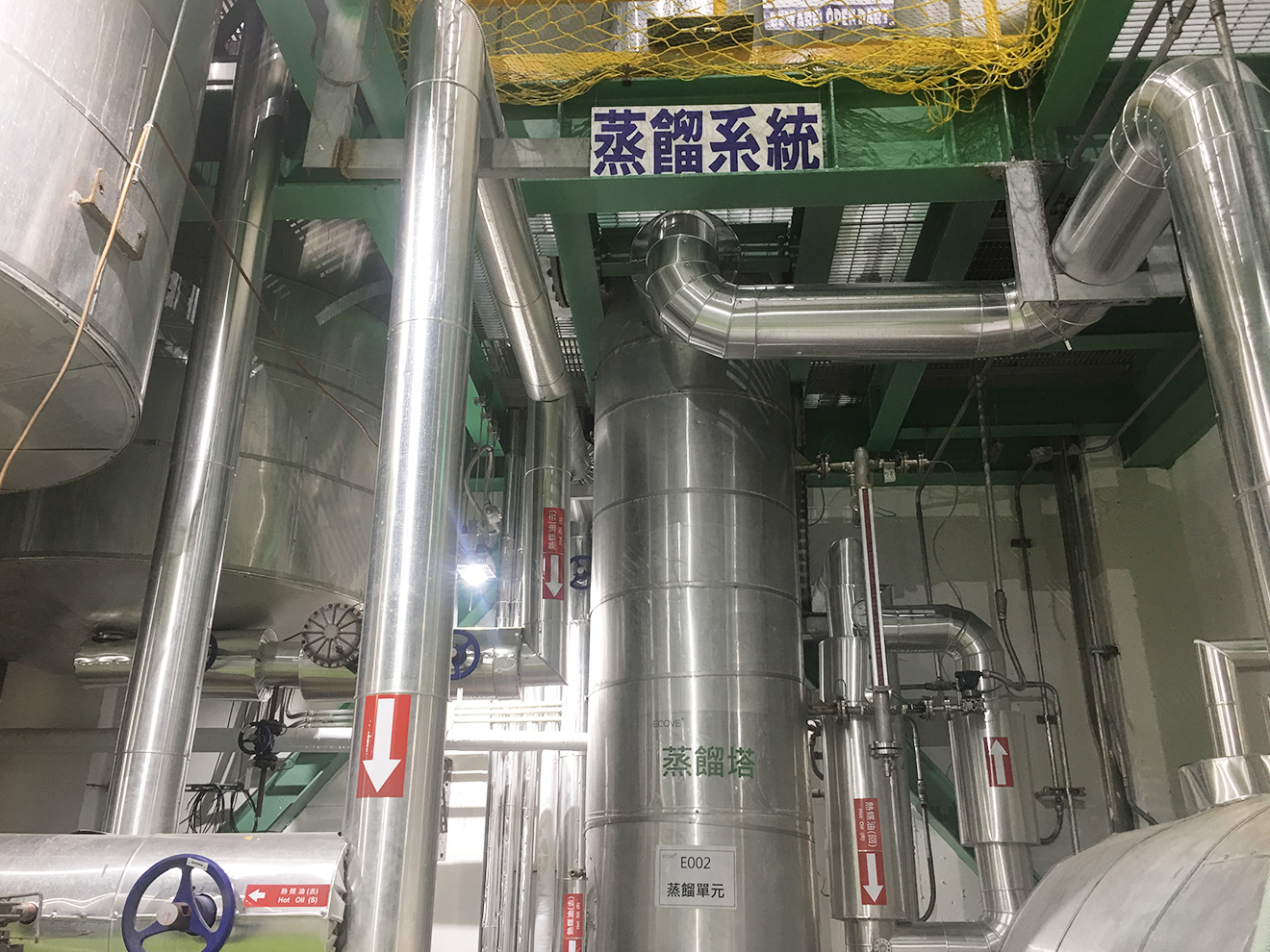
Figure 2. The distillation equipment was set in the plant after ECOVE assessed and optimized the equipment and systems of the distillation separation.
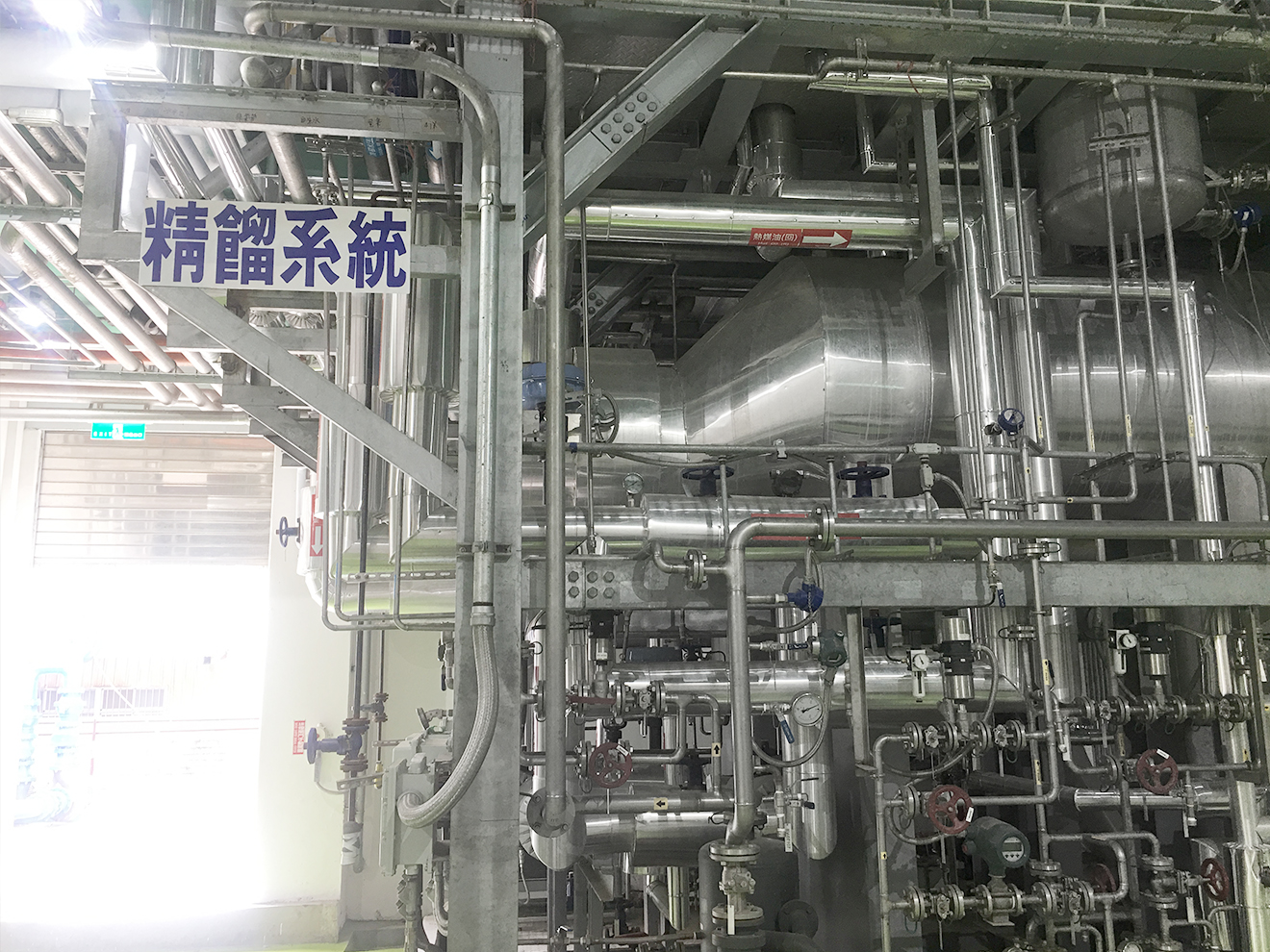
Figure 3. The distillation system was set for the plant to increase the recycling concentration of waste solvents.
ECOVE recycles the resources and reduces the pollution by following the idea of “turning the waste into the renewable resources”. In other words, ECOVE strives to convert the waste generated during the production into raw material available for enterprises and one specific example is recycling and reusing of waste solvents. ECOVE manages the waste solvents from production sources, covering from diversion planning, removing, recycling and even the process of concentration, purification and reuse. The comprehensive recycling and reusing solutions for waste solvents are offered. In the future, we will continue to enhance our recycling and reusing technologies with proficient skills and operational experience in order to make a specific contribution to maximize the benefits of resource recycling and reusing.