Key Technology
關鍵技術
Introducing Ash Cleaning Technology to Enhance Resource Cycling Efficiency
ECOVE is a practitioner of resources cycling, with over 20 years of expertise in the incineration field. We are familiar with and understand the characteristics of various moving grate incinerators and major facilities. By continually introducing new techniques and improving technology integration, we strive to optimize resources cycling efficiency. In this article, we provide an explicit example of fouling and clinker in incineration plants to demonstrate how ECOVE improves boiler efficiency and operating rates through the introduction of various ash cleaning technologies. These approaches aim to achieve benefits such as reducing carbon emissions and inhibiting the generation of air pollutants.
The Reasons for Fouling and Clinker, and the Necessity for Cleaning
The circular economy is currently recognized as the most effective way to achieve global sustainability. In a circular economy system, energy-from-waste (EfW) plants play a key role as the ultimate disposal solution when products cannot be reclaimed. By reducing waste through high-temperature incineration and converting the thermal energy generated in the incineration process into electrical power, the plants allow for an efficient conversion of waste into energy. Due to the diverse and complex composition of waste, various chemical reactions occur during high-temperature incineration, resulting in the formation of fouling and clinker. This phenomenon can adversely affect the efficiency of the incinerators and shorten the boilers’ lifespan. Processing these fouling and clinker becomes a pivotal aspect in maintaining the incineration and heat exchange efficiency of the boiler. What causes fouling and clinker to form? When examining the incineration system of an EfW plant's boiler, we can see that the waste first enters the furnace through the feed hopper. Since the gas temperature in the furnace is the highest, the ash particles generated after incineration flow through the first, second, third, and fourth passes of the flue gas. As the flue gas temperature gradually decreases, both coarse and fine particles begin to form a thin layer of ash. The high temperature causes the edges of ash particles to bond with each other, leading to an increase in the thickness of clinkers. This particularly occurs at the bends of the second and third passes, resulting in the formation of fouling and clinker, often obstructing the flow of flue gas and increasing the differential pressure between the inlet and outlet of the superheater bundles. The rise in the superheater surface temperature causes a decline in heat exchange efficiency and contributes to operational difficulties in the boiler. To address the issue of fouling and clinker, ECOVE has been gradually introducing various ash cleaning technologies since 2010.
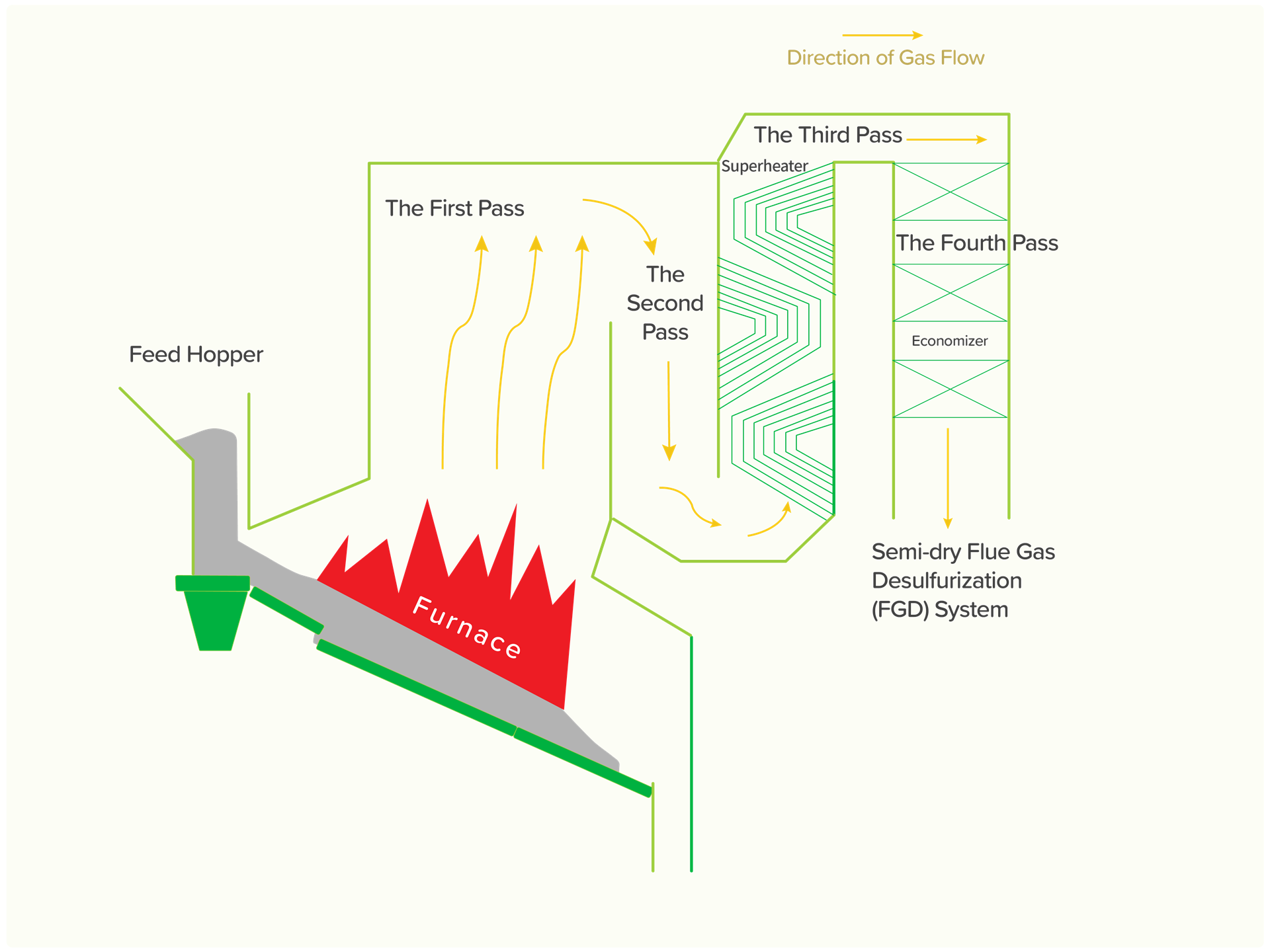
Schematic Diagram of Incineration Plant Boiler System

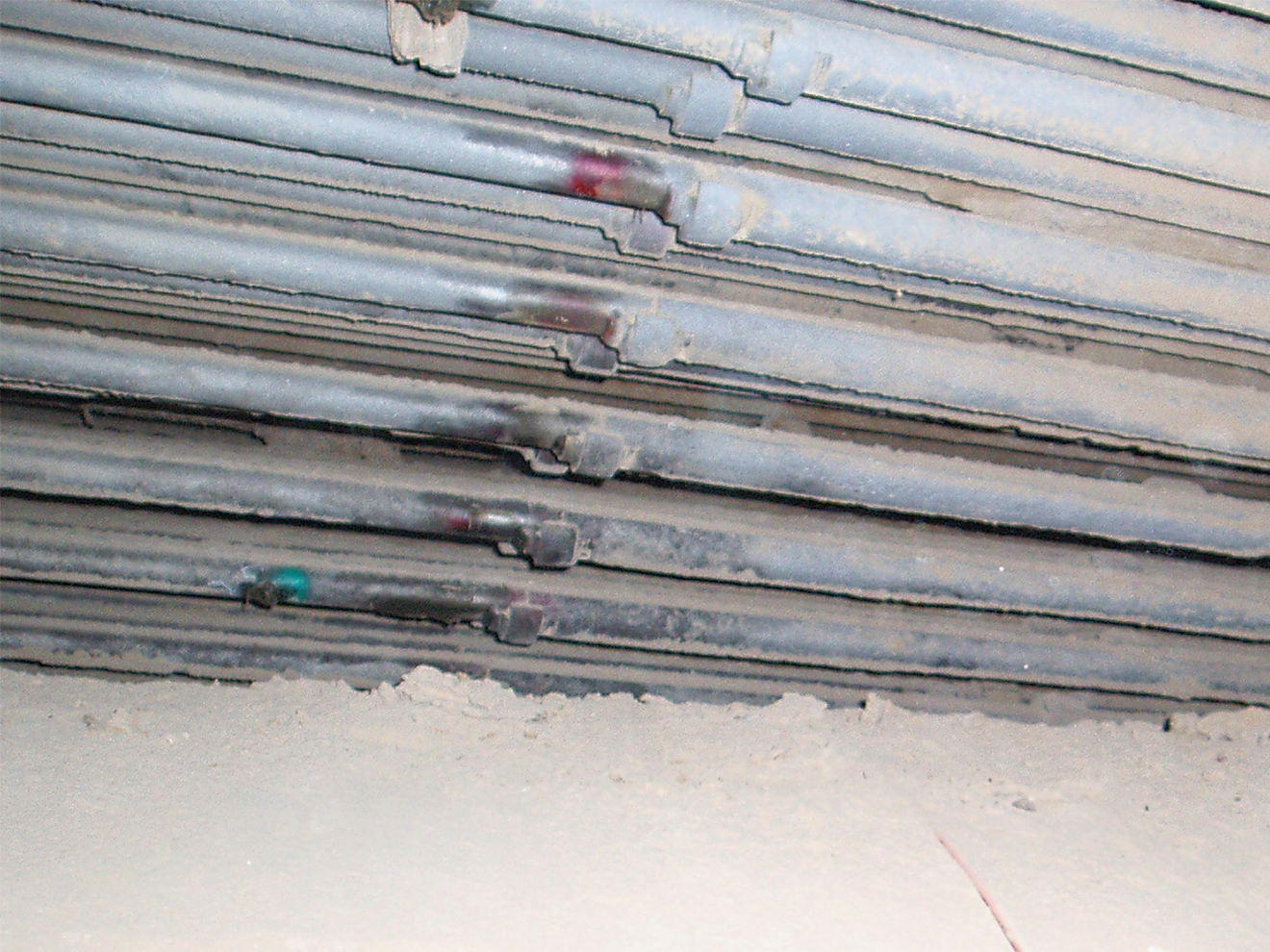
Early Ash Cleaning Technique
In the past, ash deposit removal from boiler flues primarily relied on two techniques: superheated steam soot blowing and rapping. These methods entailed manual ash cleaning operations during incinerator shutdown. In the superheated steam soot blowing method, a motor drives the screw of the steam soot blower forward, enabling the steam nozzle to extend into the flue and effectively blow away the fouling and clinker from the tube surfaces. Conversely, the rapping technique is suitable for cleaning horizontal passes (as depicted in the image below). This technique involves transmitting energy to the tube bundle with a hammer, causing the fouling and clinker to dislodge and fall. However, these two methods can only slow down the rate of fouling and clinker. Incineration plants still need to shut down periodically for manual ash cleaning, usually every six months. During the manual cleaning process, workers enter the superheater area with tools to manually remove the fouling and clinker. This adds to labor requirements and poses potential safety concerns. When the spacing between the superheater bundles in the boiler is excessively narrow, this may accelerate the rate of ash accumulation, leading to an increase in the frequency of shutdowns for cleaning. The recurring start-up and shutdown of the incinerator may result in energy loss, leaving insufficient time for ash cleaning due to the time pressure of waste processing, leading to an inefficient result of ash cleaning.
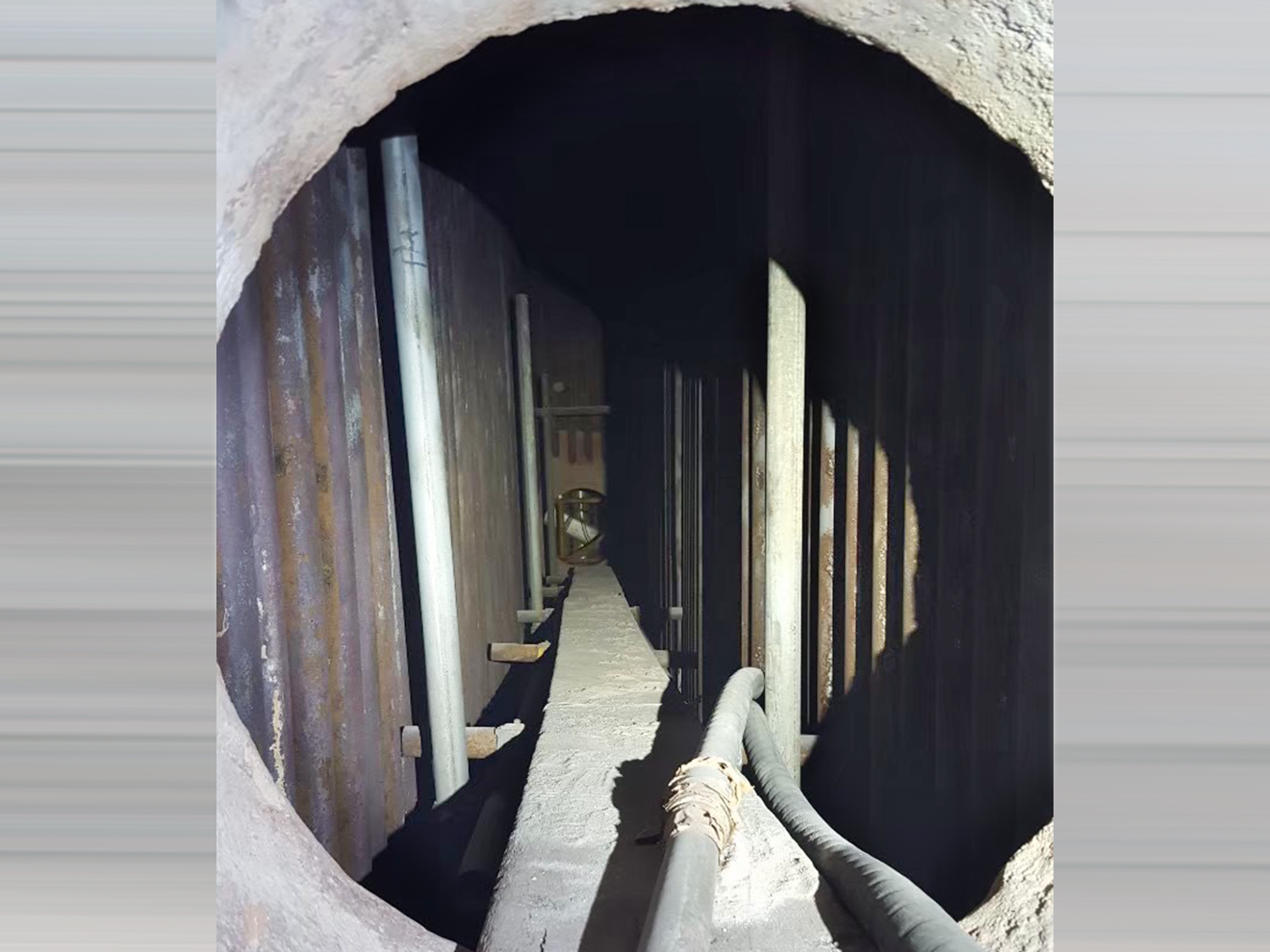
Horizontal Flue
ECOVE’s Implementation of Ash Cleaning Technologies and its Applications
ECOVE currently operates 9 EfW plants in Taiwan. Since 2010, to improve the operational limitations of traditional ash cleaning techniques, ECOVE progressively introduced various ash cleaning technologies based on factors such as the design condition of each plant (as shown in the diagram below).
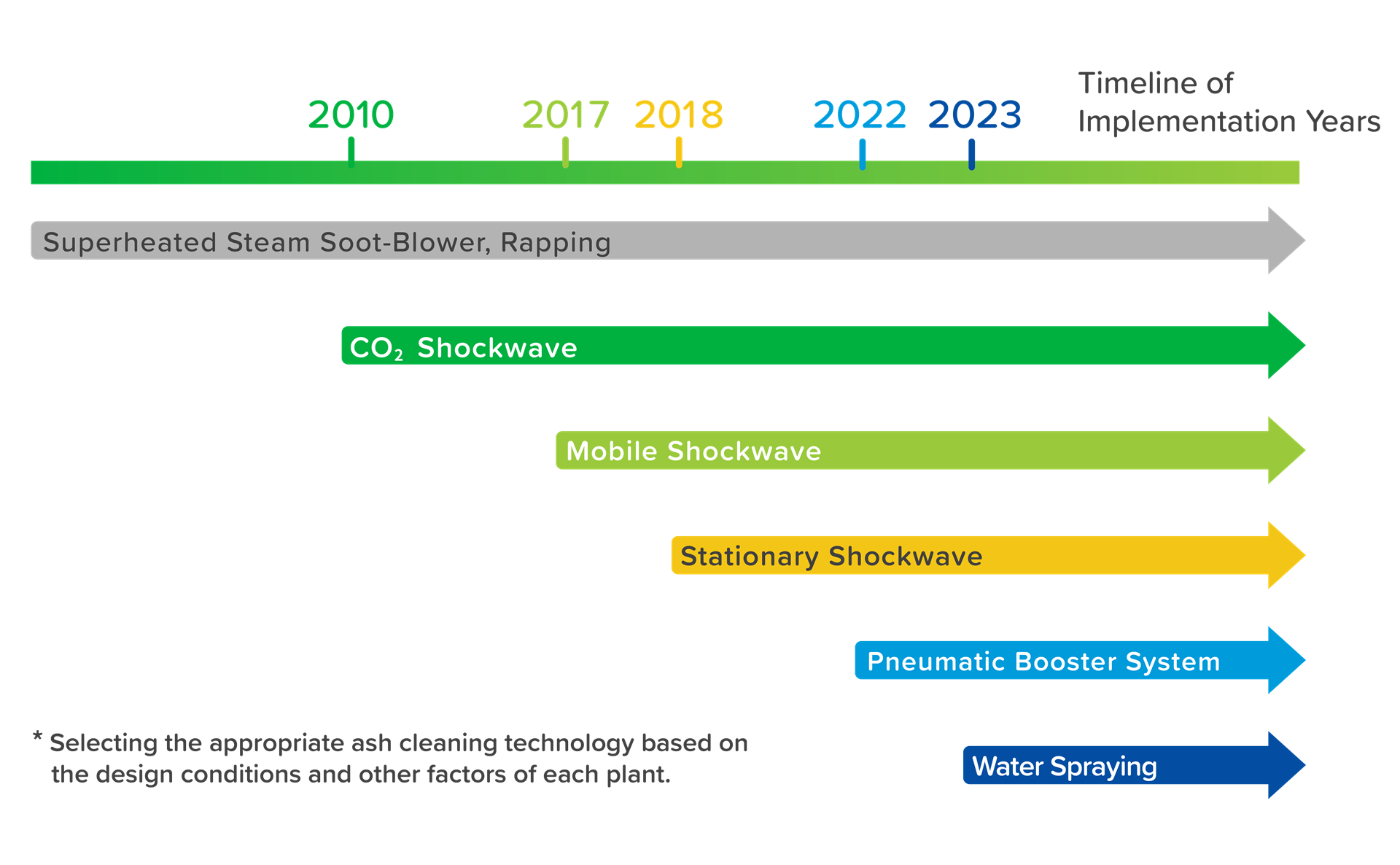
Timeline of ECOVE Implementing Ash Cleaning Technologies
After years of operation, most of ECOVE’s EfW plants primarily utilize the stationary shockwave technique, complemented by the mobile shockwave to enhance the effectiveness on regional ash cleaning. In 2023, ECOVE introduced the new "water-spraying" technique. However, considering that most EfW plants are nearing their limits in terms of steam handling capacity, installing a water-spraying facility can only marginally increase steam production. Due to considerations related to boiler tube coating applicability, the water-spraying technology is currently implemented and constructed exclusively in the newly built Taoyuan Biomass Center. The following paragraph will provide clear outlines regarding characteristics of each ash cleaning technology:
- In 2010, ECOVE introduced the CO2 shockwave technology: A customized lance was inserted into the furnace, injecting liquid CO2 into a disposable chemical heater inside the lance. Upon detonation, the heater is activated, instantly vaporizing the CO2 and generating high-pressure CO2 gas. The pressure shock wave accompanying the explosion is utilized to remove fouling and clinker.
- In 2017, ECOVE introduced the mobile shockwave technology: A special container is fixed at the front-end of the ignition lance. The lance is then inserted inside the boiler to where it requires cleaning, transferring gas to the front-end then detonated and send off shockwaves.
Although both techniques are able to enhance regional cleaning effects, the execution process still involves the opening and closing of manholes, leading to concerns such as personnel safety and the entry of external cold air. This also relies on the assessment of fouling and clinker, as ash cleaning can be carried on if the ash conveyor has enough capacity. However, when the dislodged ash exceeds the load capacity, the inspection holes of the ash conveyor need to be opened manually to check how on the ash discharge condition, preventing ash bridging that could lead to the boiler’s shutdown.
- In 2018, ECOVE introduced the stationary shockwave technique: This method utilizes high-pressure cylinders containing an air mixture consisting of methane and oxygen, generating pressure pulses that can dislodge fouling and clinker. The method exhibits significant ash cleaning results, effectively removing ash from concealed and hard-to-clean areas. By scheduling a periodic shockwave frequency, ECOVE is able to reduce the degree of fouling and clinker, it helps avoid ash bridging and reduces the frequency of shutdowns for cleaning.
- In 2022, ECOVE introduces the pneumatic booster system: About one-third of the air mixture remains inside the gas cylinder after the stationary shockwave procedure. To effectively utilize the remaining gas, ECOVE set up a pneumatic booster system, with a reciprocating pneumatic booster that automatically starts and stops by mechanism. When the compressed air in the gas cylinder is under target pressure, the system initiates operation, and ceases when achieving target pressure. After various testing, the system was applied on site and obtained patent approval in 2023. If a plant site allows for the installation of natural gas pipeline after assessment, the gas can be obtained through piped delivery, eliminating the inconvenience of replacing gas cylinders.
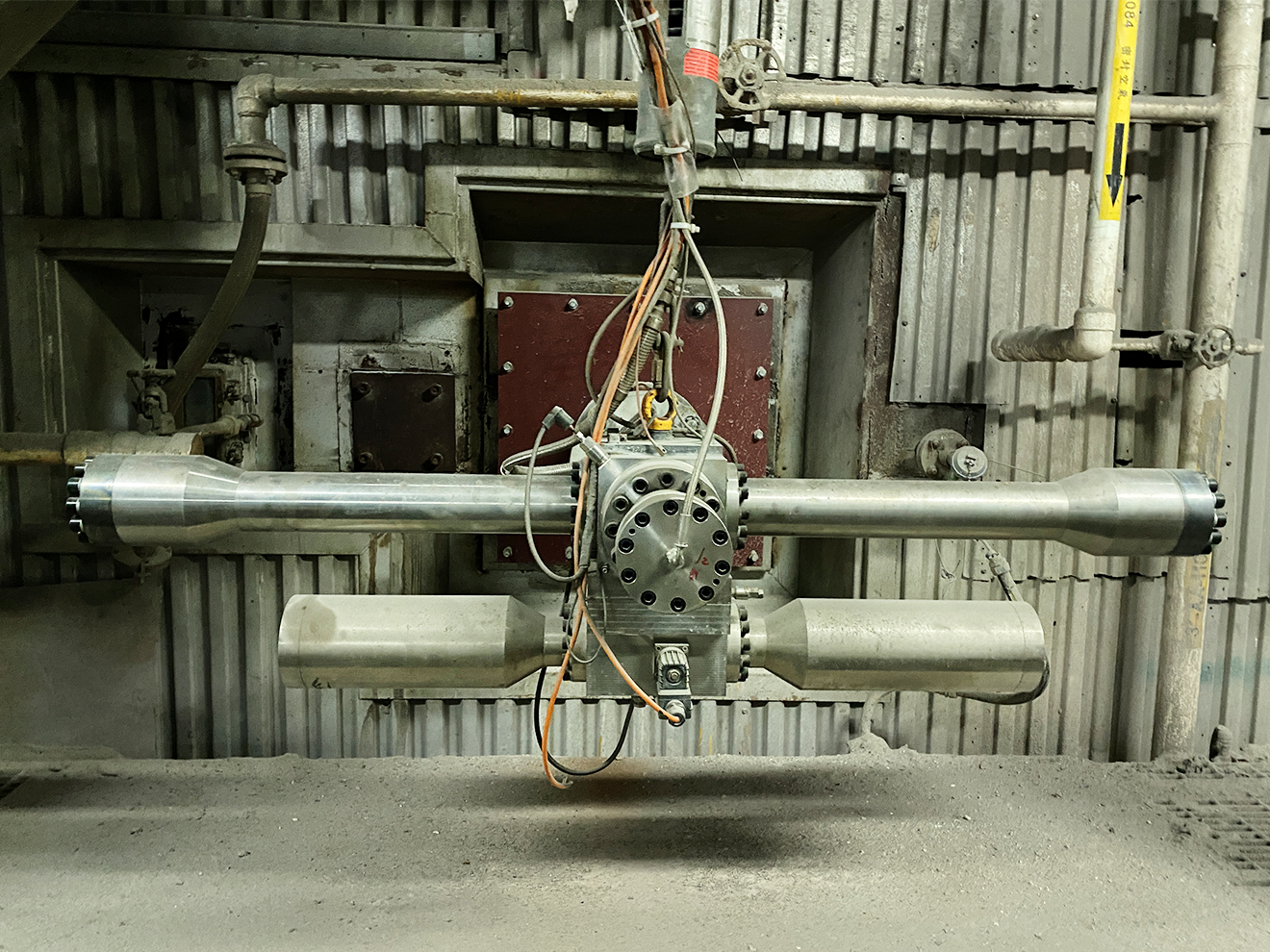
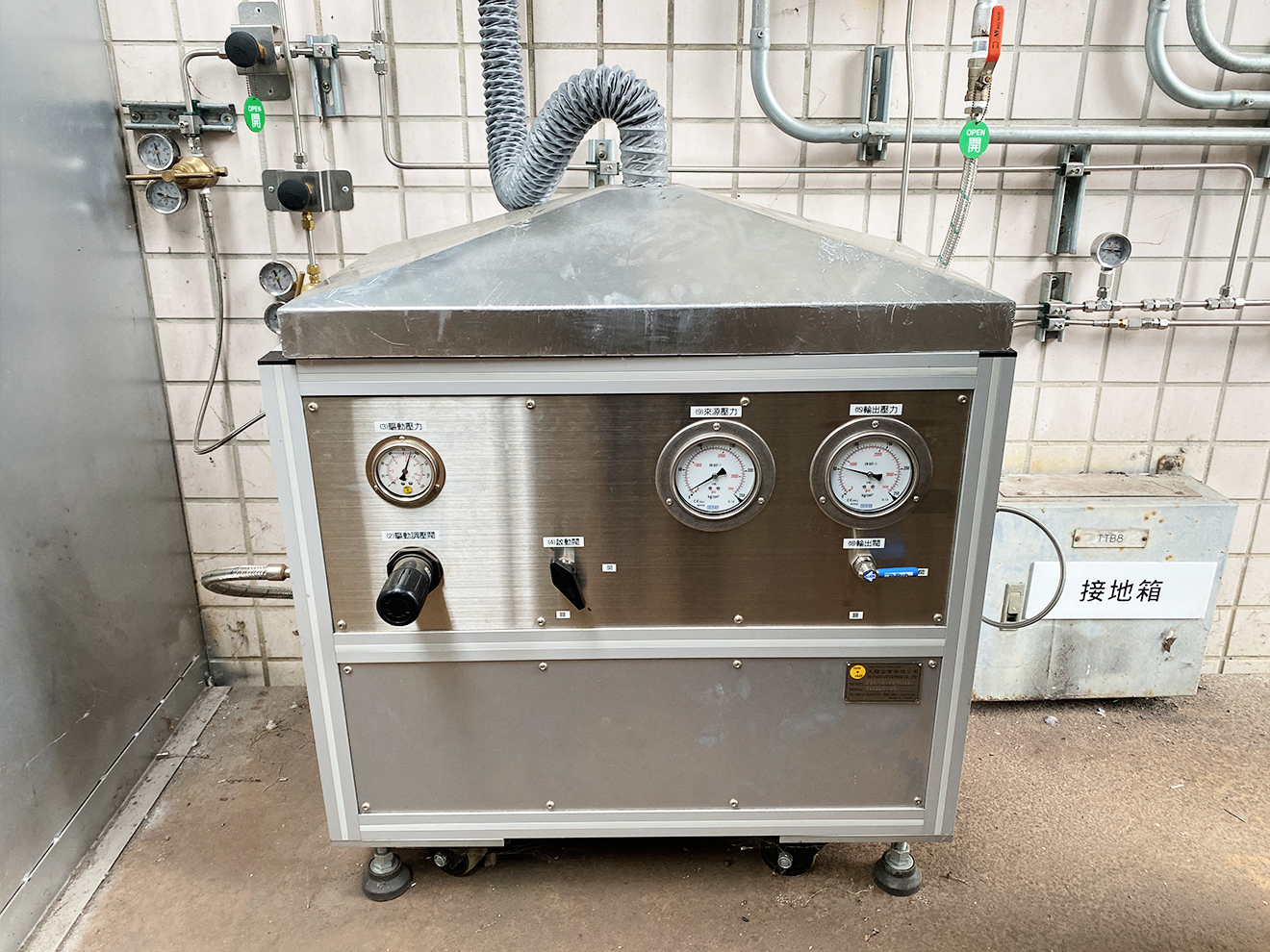
- In 2023, ECOVE introduced the water-spraying technique: With elevating the waste-to-energy efficiency being a part of Taiwan’s Net-Zero Pathway, ECOVE is paying close attention to technologies that allow stable heat transfer efficiency of the boiler wall tube in the secondary chamber. In the past, the fouling and clinker on the water-cooled walls of the secondary chamber caused lower heat transfer efficiency, resulting in elevated boiler temperatures and a decrease in boiler efficiency. Moreover, increased boiler temperature not only accelerates downstream wall tube corrosion, fouling, and clinker, but also elevates the rate of nitrogen oxide generation, contributing to an increase in emissions of air pollutants. To address this issue, ECOVE installed a water-spraying system on the top of the secondary chamber. With an adjustable system, the descending water pipes enter the boiler, spraying water droplets. When the water droplets touch the surface of the fouling and clinker, they evaporate and expand in volume, effectively removing the ash. This process helps lower the boiler temperature while maintaining a certain level of heat exchange efficiency, further suppressing the emission of air pollutants.
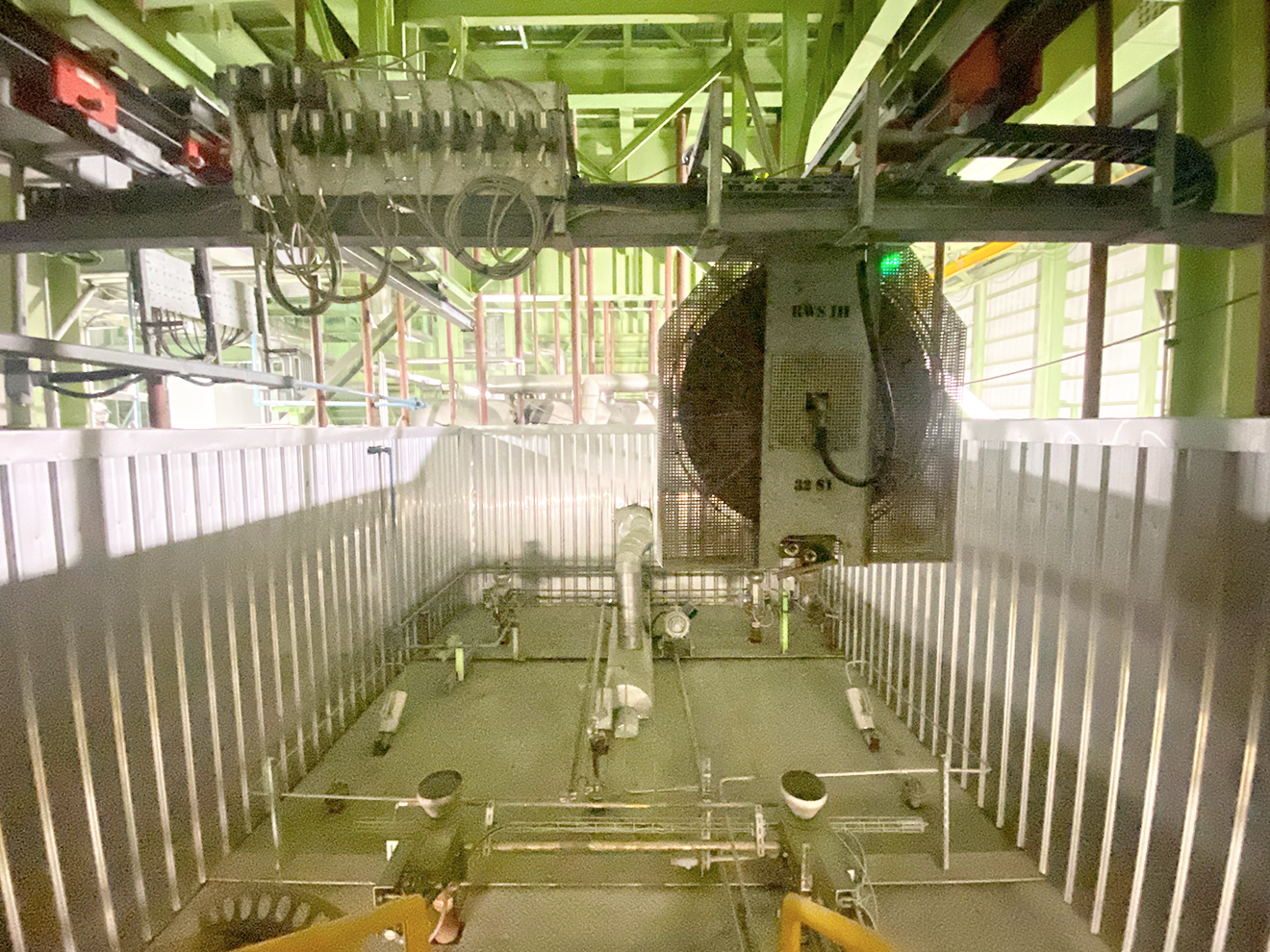
Water-Spraying Equipment
Enhancing Synergies of Circular Economy Through Innovation and Improvement
Currently, all the EfW plants in Taiwan are operating at their full capacity. Therefore, it is crucial for each EfW plant to apply suitable ash cleaning technology judging on factors such as their design conditions and more. By selecting the appropriate cleaning methods, boiler heat exchange efficiency can be stabilized, facilitating effective waste heat recovery. This, in turn, reduces energy demand and consequently lowers carbon emissions. Moreover, it helps suppress the generation of air pollutants. As ECOVE strives to innovate through ash cleaning technology, it hopes by integrating the principle of resource cycling, these technologies will expand the effectiveness of circular economy and achieve net-zero emissions in practice. By integrating the principle of resource cycling, ECOVE aims to innovate through ash cleaning technology, seeking to enhance the synergy of the circular economy and contribute to achieving net-zero emissions in practice.