Innovation
企業創新
Revitalization of an Old Plant: Xizhou EfW Plant Embarks on a New Journey
The Xizhou Energy-from-Waste (Incineration) Plant in Changhua County has been in operation for over 20 years and is in urgent need of several crucial equipment upgrades and overhauls. In order to stabilize the plant's operation and improve operational efficiency, the Environmental Protection Bureau of Changhua County Government conducted an open tender in 2021 for a 15-year operation and upgrade project for the entire facility. With over 20 years of experience in the field of incineration, ECOVE excels in operational management, annual maintenance, and system enhancement, and offers tailored equipment upgrade project services designed to match the specific features of furnaces. After evaluation, ECOVE successfully won the tender. In this article, we will discuss how ECOVE achieves new value for this aging incineration plant through the implementation of three key principles: Recovery and Ensuring Incineration Capacity, Enhancing Energy Efficiency, and Improving Pollution Control Effectiveness.
Recovery and Assurance of Incineration Processing Capacity
The Xizhou Plant plays a vital role in processing municipal waste from Changhua County and supports the county government's policies promoting resource utilization and zero waste. Similar to many other energy-from-waste plants across Taiwan, it has been in operation for many years, and its system equipment has reached the end of its service life with no spare parts available. To boost its operational stability, ECOVE has planned and is implementing various hardware and software equipment upgrades, as detailed below: I.Software Upgrade the weighbridge system (including the addition of uninterruptible power supply system and lightning protection system) and implement a surveillance system in public areas such as the weighbridge and platform to enhance information security and maintain facility safety. Introduce a high-performance license plate recognition system integrated with intelligent management for round-the-clock stringent control of waste entry to ensure the security of government property.
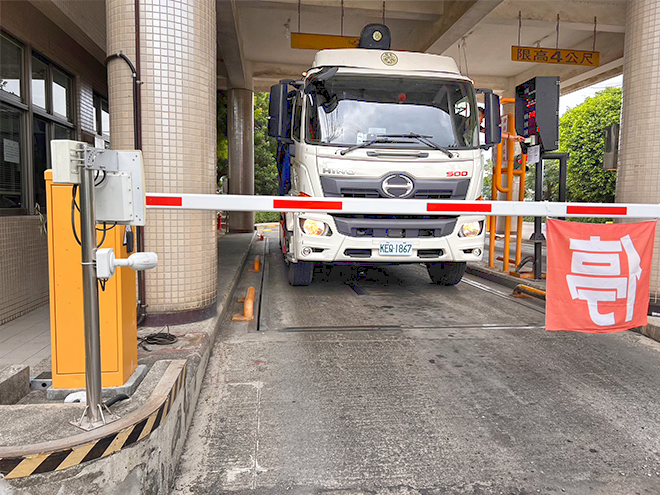
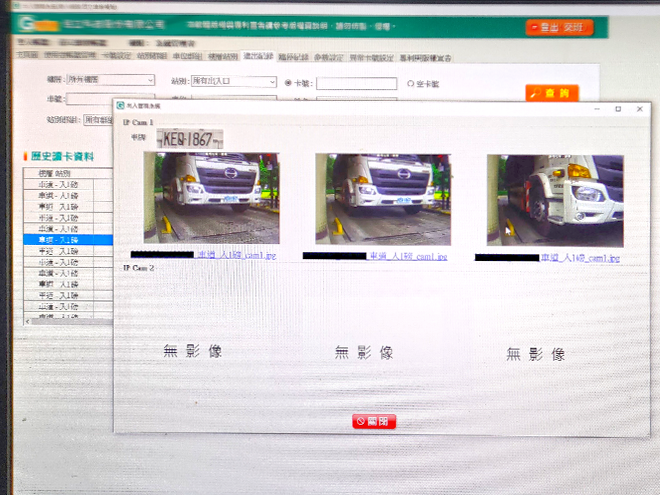
II.Hardware Upgrade or install a variety of critical waste feeding and incineration operation-related equipment, including large-scale waste shredders, waste cranes, bottom ash cranes, boiler water wall tubes, and stationary shockwave ash cleaning devices for boiler flue gas ducts, to enhance operational stability and ensure incineration processing capacity. The expected performance for the upgrade of boiler water wall tubes and the addition of a fixed ash cleaning device for the boiler flue gas duct is specifically introduced below.
- Upgrade boiler water wall tubes: The long-term exposure to high-temperature exhaust gases has led to thinning of the boiler water wall tubes. Additionally, significant changes in the nature of the waste in recent years have increased the unplanned furnace shutdown risk and operational costs. For the upgrade and overhaul, we employ the latest Inconel 625 high-alloy cladding technology on the boiler tubes. Leveraging historical statistical data, we are focusing on replacing the top rear walls of the first and second boiler flues located in areas with a high risk of thermal erosion. It is expected that the thinning rate will be decreased by 97% (thinning rate less than 0.1 mm/year), resulting in a projected service life of over 10 years.
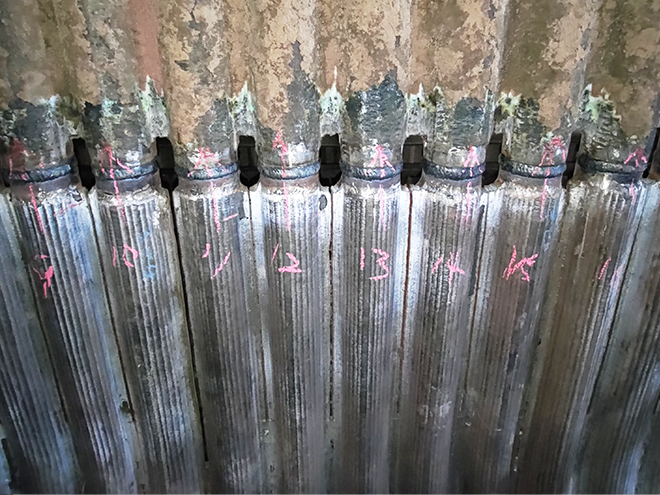
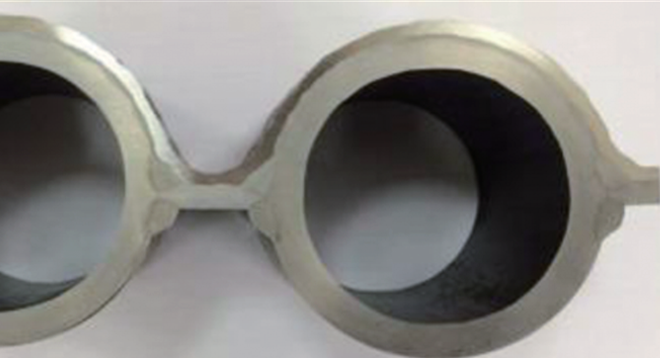
- Installation of stationary shockwave ash cleaning device: The original plant design employed soot blowers in conjunction with high-pressure steam for ash cleaning in the third boiler flue. However, steam serves as the power source for the generator, and while the use of soot blowers indirectly increases boiler efficiency, it directly impacts electricity generation capacity. Therefore, the latest generation of fixed acoustic cleaning devices have been selected to replace all soot blowers in the third boiler flue. This not only reduces the usage of high-pressure steam but also provides a more comprehensive and effective ash cleaning solution for the flue.
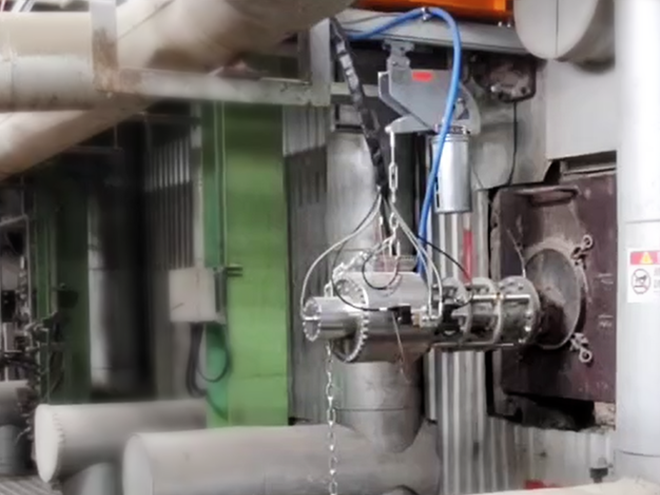
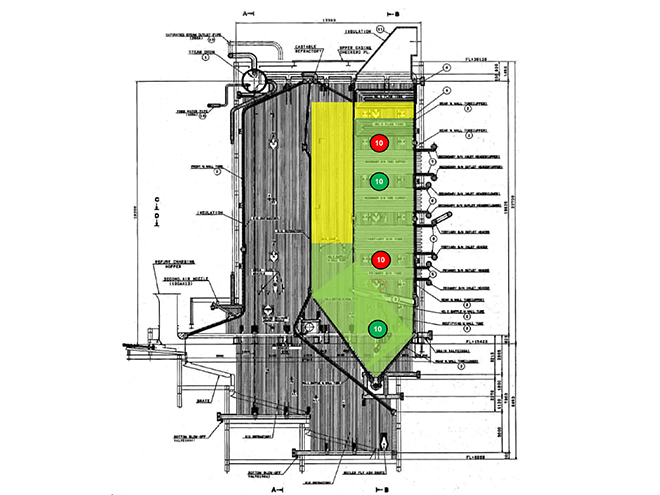
III.Equipment Deterioration Assessment In consideration of the stability of the supply of critical components in various system equipment within our plant, a comprehensive review is being conducted, encompassing issues related to occupational safety, fire prevention, and equipment deterioration assessment. Through reinforcement, replacement, and optimization of these components, the equipment's functionality is being restored. The planned work items include the semi-dry scrubber atomizer booster, induced draft fan impellers and associated bearings, bearing housings and shafts, detectors for turbine generator shaft misalignment and vibration, automatic voltage regulators for generators, excitation machine control circuit boards, cast resin transformers, and fire alarm systems.
Enhancing Energy Efficiency
Net zero emissions has become a global imperative, and through the equipment inspection and upgrade outlined below, we anticipate a reduction in energy consumption of 18% and an increase in electrical efficiency of over 25%, effectively boosting the sale of renewable energy. I.Upgrade and Install Variable Frequency Drives (VFDs) The upgrade project includes the installation of variable frequency drives (VFDs) for the waste crane hoist trolley, main hoist, and bottom ash crane hoist trolley, along with the main hoist VFDs. The addition of VFDs for the primary and secondary fans, as well as the air compressor, is part of the expansion project, improving operational efficiency and contributing to achieving energy-saving objectives. II.Upgrade to IE3 High-Efficiency Motors By upgrading high-power motors such as those in the primary and secondary fans, air compressor motors, and equipment cooling water motors to IE3 high-efficiency motors, we fundamentally increase motor energy utilization to over 95%, thereby reducing energy waste. III.Utilization of Advanced Materials and Technologies The blades of the air-cooled condenser have been upgraded to a composite material, fiber-reinforced plastic (FRP). In addition to being lightweight, the increase in blade count from 10 to 12, along with the ability to design attack angles and blade curvature, offers greater energy efficiency. IV.Utilization of High-Efficiency Transformers Traditional high-energy-consumption silicon steel core transformers are replaced with transformers using amorphous alloy as the core material. It is anticipated that iron loss will decrease from 29.5 kW to 7.0 kW, representing a reduction of approximately 75%.
Enhancing Pollution Control Effectiveness
In anticipation of the stricter nitrogen oxides (NOx) emission standards to be enforced after June 2025, our plant has outlined the following improvements aimed at reducing NOx emission concentrations: I.Integrating Computational Fluid Dynamics (CFD) simulation technology for the upgrade of Selective Non-Catalytic Reduction (SNCR) equipment Currently, all domestic energy-from-waste plants in the country employ selective non-catalytic reduction (SNCR) for NOx gas pollutant removal. The efficiency of SNCR is contingent on the combustion temperature within the boiler and the reaction with chemical agents, involving multiple variables such as boiler size, structural design, operating parameters, and waste characteristics. In order to maximize the exposure of the reaction reagent to the optimal reaction temperature, the ECOVE team utilizes advanced computer simulation analysis techniques, incorporating professional Computational Fluid Dynamics (CFD). This is employed to assess and plan the optimization design parameters for SNCR, such as injection quantity and injection location. It is expected that this optimization will lead to a reduction in NOx emission concentrations to below 70 ppm, which represents a reduction of over 17% compared to the Ministry of Environment’s (formerly the Environmental Protection Administration) 2020 announcement of the pollutant emission standard for NOx concentration at 85 ppm for existing fixed pollution sources in the Tier 3 Control Zone. It also includes the functionality of automatically adjusting the chemical reagent injection quantity based on values detected by Continuous Emission Monitoring Systems (CEMS) to enhance the efficiency of chemical reagent utilization. II.Updating the 24-hour boiler outlet CEMS to optimize the effectiveness of pollution control equipment by monitoring and analyzing pollutant emission concentrations
Improved Equipment Performance Recognized and Appreciated by Both the Client and the Regulatory Authorities
In line with ECOVE's commitment to the three core principles of Recovery and Ensuring Incineration Processing Capacity, Enhancing Energy Efficiency, and Improving Pollution Control Effectiveness, this equipment upgrade and overhaul project, leveraging innovative engineering techniques, has yielded the following operational and performance results compared to pre-upgrade conditions in 2021.
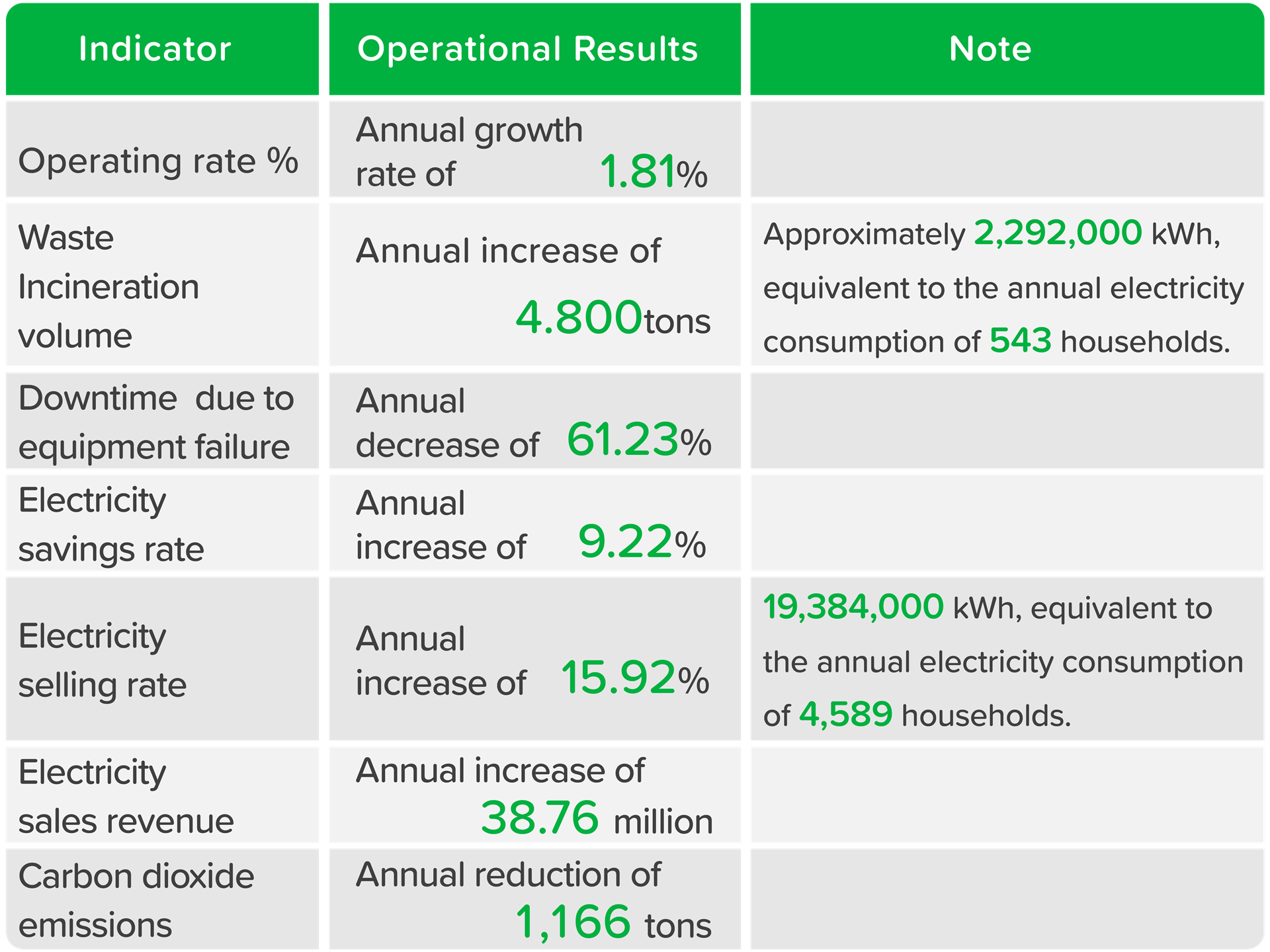
Operational Results Summary Following the Xizhou EfW Plant Upgrade and Refurbishment
Furthermore, in alignment with the government's net-zero carbon emissions policy, ECOVE, during the execution of this project, opted for government-certified green and environmentally friendly products. This decision, while enhancing efficiency, also prioritized carbon reduction, allowing us to fulfill our corporate social responsibility as a responsible corporate citizen. As a result, we were honored with the recognition as an Outstanding Green Procurement Unit by Changhua County. ECOVE's wealth of experience and capabilities have led to significant progress ahead of the project schedule. Our exceptional performance has earned us the "Business Excellence Award" in the 2022 Environmental Protection Administration's audit and assessment. In response to the fact that many energy-from-waste plants across Taiwan have reached their operational limits, ECOVE will actively participate in the government's "Diversified Waste Treatment Program." We aim to assist aging EfW plants in upgrading their facilities, thereby addressing the critical issue of waste management for local governments and clients.

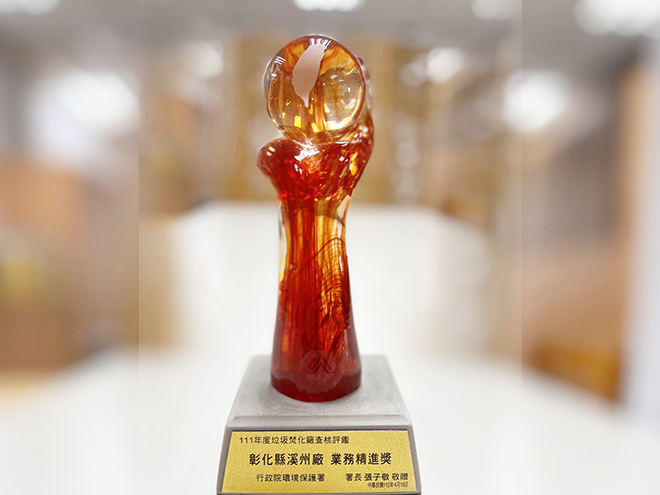