Policies and Committees
ECOVE's Health Safety and Environment (HSE) policy is based on fulfilling environmental protection obligations and creating a safe and healthy work environment. It aims to safeguard the physical and mental well-being of employees and contractors, ensuring a secure and hazard-free work environment.

Regarding occupational safety and health committees, among ECOVE and its subsidiaries, ECOVE Environment Service Corp. and ECOVE Waste Management Corp. have reached the statutory size and set up committees, while ECOVE, ECOVE Wujih Energy Corp., ECOVE Miaoli Energy Corp., and ECOVE Solvent Recycling Corp. have not reached the standard and therefore have not set up committees. However, they still follow the spirit of the system, and the employees can participate in the supervisors' weekly or monthly meetings regularly, and communicate with each other on occupational safety and health issues in the agenda, and G.D. Development Corporation, although it does not reach the statutory size, still follows the spirit of ISO 45001 to set up committees. The Occupational Safety and Health Committees of ECOVE Environment Service Corp., ECOVE Waste Management Corp., and G.D. Development Corporation are convened quarterly, and the results of the meetings are announced through the website or bulletin boards to convey the spirit and content of the Occupational Safety and Health Committees to the employees and non-employees, among which the ECOVE Environment Service Corp. Committee has 36 members, including 13 labor representatives, accounting for 36% of the total number of committee members, with the president serving as the chairperson of the committee; the ECOVE Waste Management Corp. Committee has 10 members, including 4 labor representatives, accounting for 40% of the total number of committee members; and the G.D. Development Corporation Committee has 8 members, including 3 labor representatives, accounting for 38% of the total number of committee members.
Organizational chart of OSH Committee at ECOVE Environment Service Corp
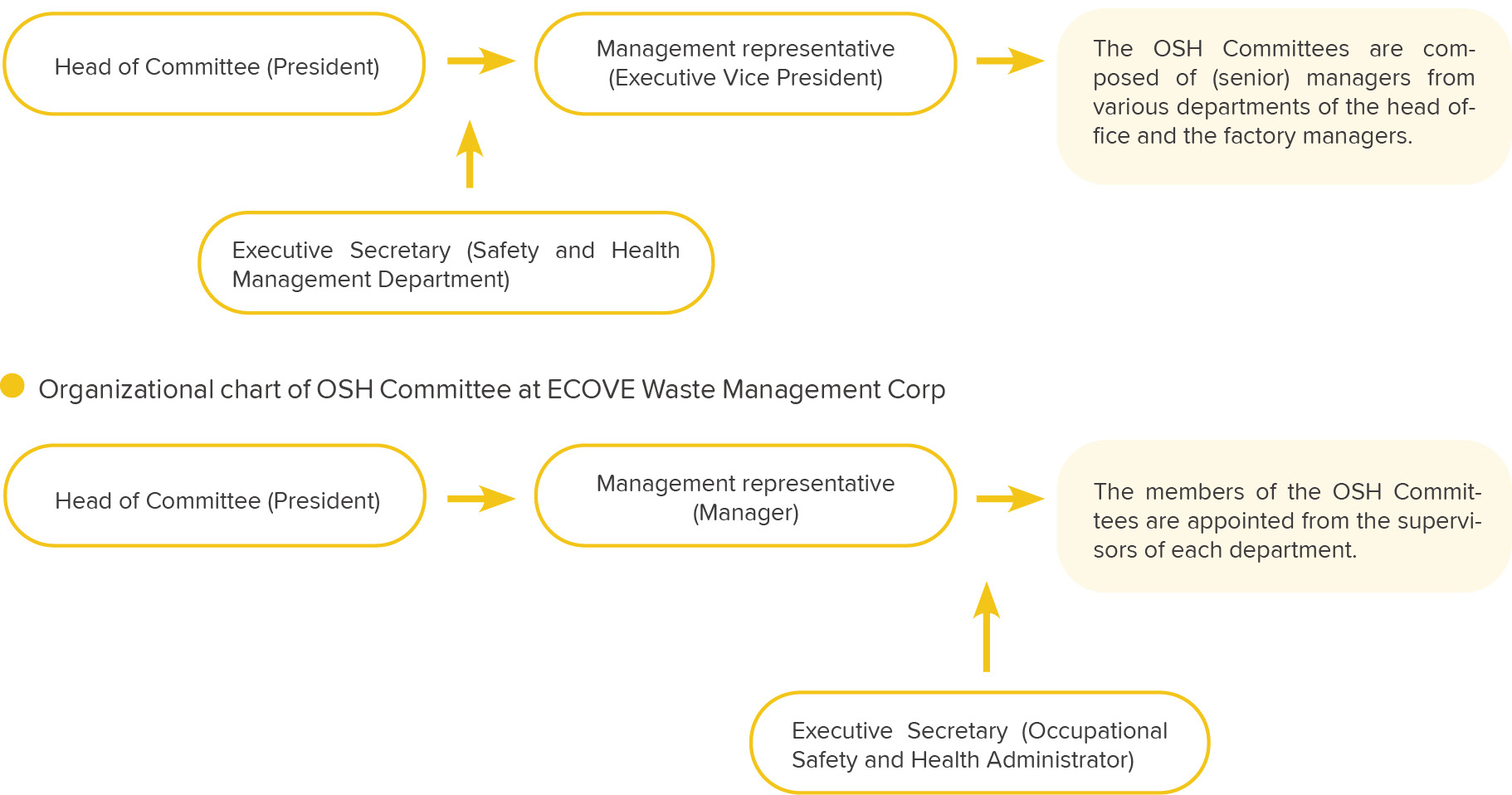
Organizational Chart of ECOVE Solar Energy Corporation Occupational Safety and Health Committee
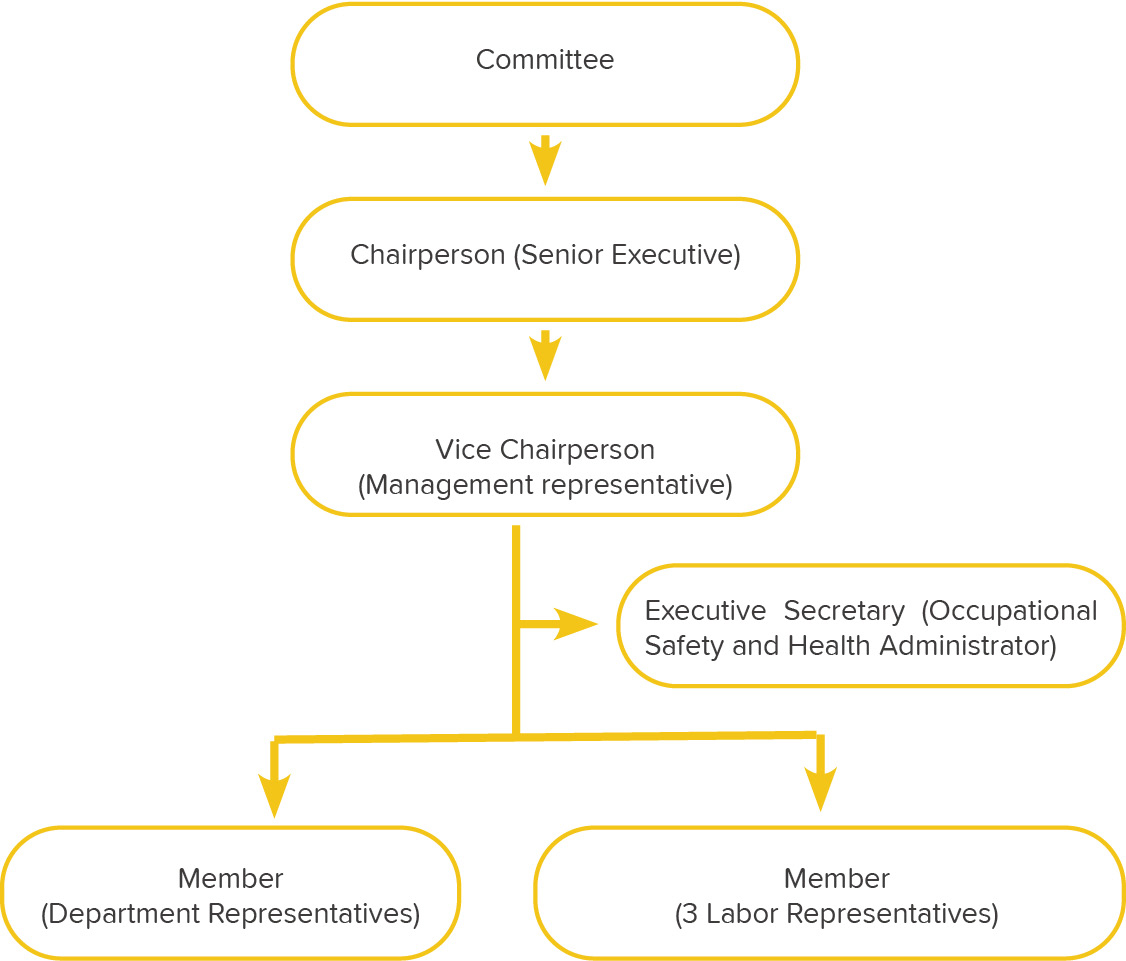
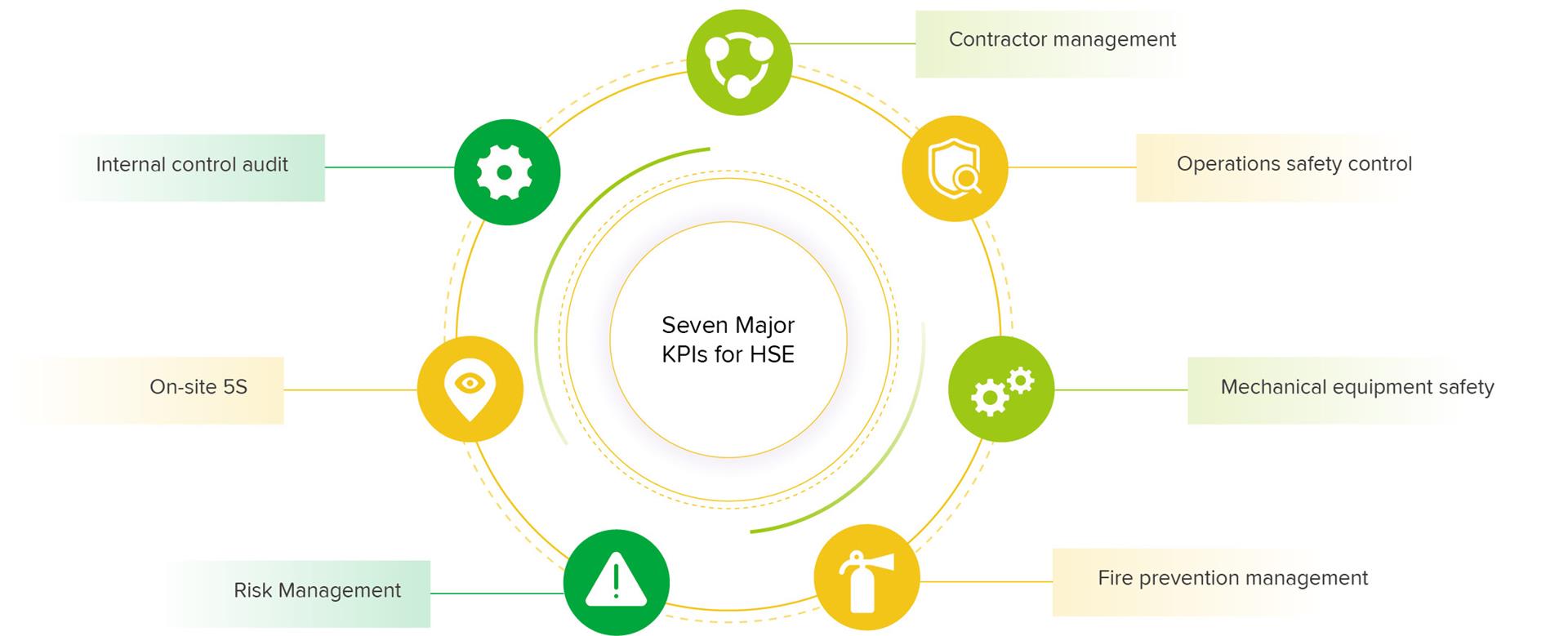
Risk Evaluation and Operations Safety Control
ECOVE and its subsidiaries employ a risk management approach to occupational safety and health, which involves categorizing risks through a Risk Management Committee. The identified risk categories include information security risk, HSE risk, operational risk, quality management risk, and climate change risk. HSE risks are assessed through occupational safety and health management system at least twice a year for each operation process, chemicals, hand tools, and environmental exposures, etc., and operation standards and regulations are formulated and publicized according to the level of risk assessment, and if any risk exists, it can also be responded to through the employee communication platform on the EIP (including employee mailboxes, proposals for improvement, and reporting platforms), and the work hazards notifier can be protected anonymously, and at the same time, through the on-site inspection, the reasonableness of the operation standard is reviewed in order to achieve the suitability of the contents of the operation standard.
HSE risk assessment process flow
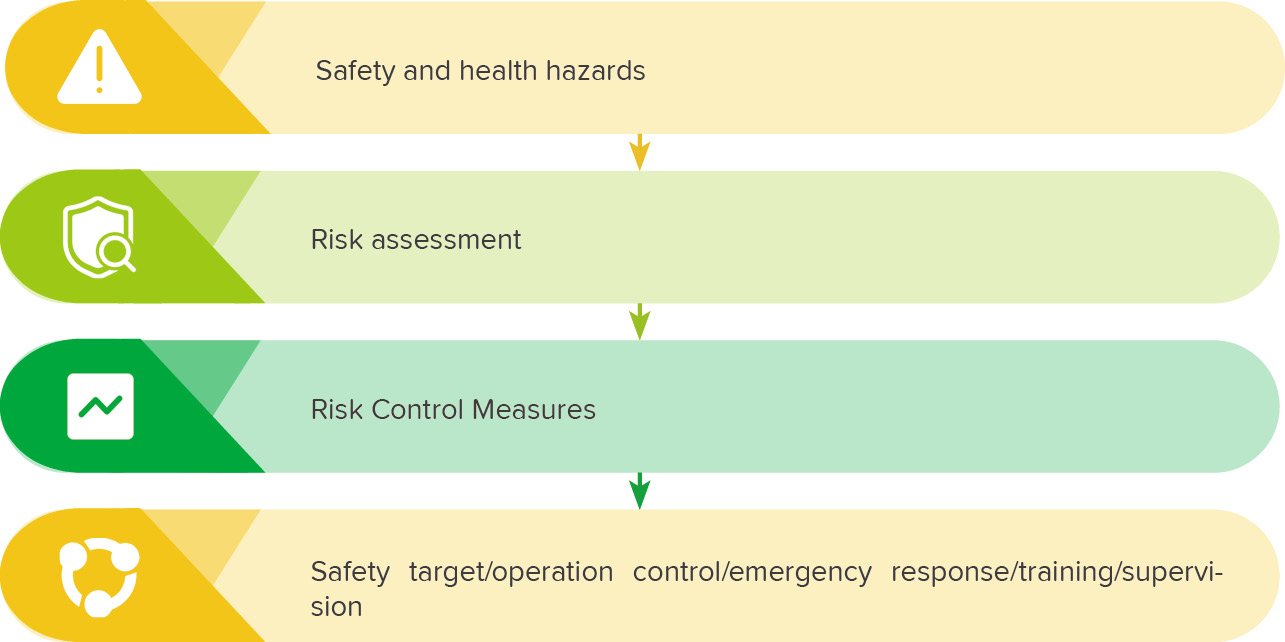
After evaluating through the management system, high-risk and hazardous tasks such as rotating equipment maintenance, pipeline maintenance, hot work operation, confined space operation, elevated (high-altitude) operation, hanging operation, and electrical operation are governed by specific operational safety control regulations. Daily work assignments are managed through the MMIS (Maintenance Management Information System) developed by ECOVE Environment Service Corp. During the morning meeting, a Job Safety Analysis (JSA) is conducted to raise awareness of hazards. Employees are required to apply for work permits based on the job content risks and operational safety control regulations. The three parties involved, including the operators, maintenance personnel, and safety personnel, visit the site together to verify and carry out procedures such as power shutdown, isolation, lockout, and tagging. Only after confirming the absence of any potential hazards can the work commence, aiming to achieve the goal of zero accidents during operations.
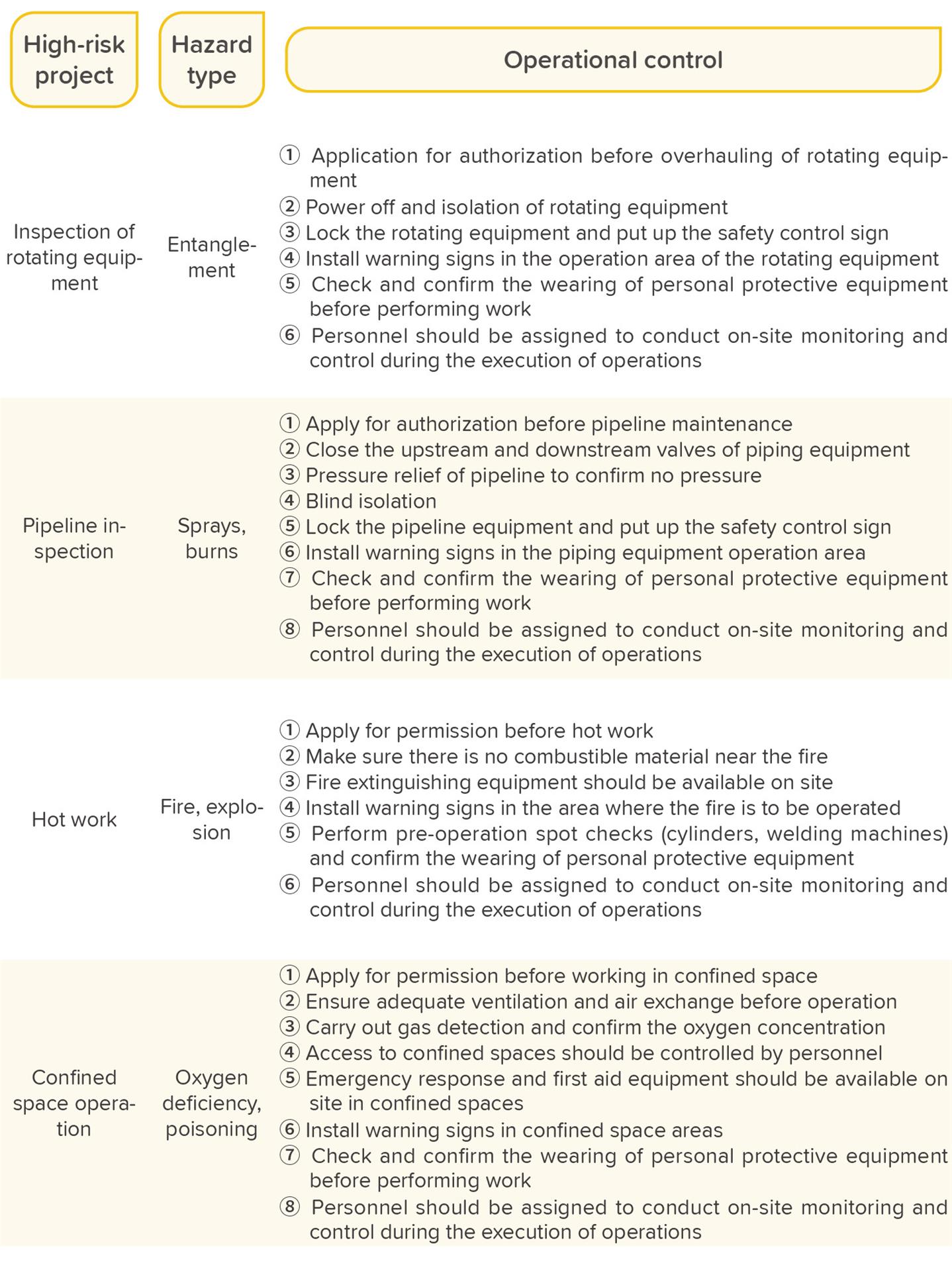
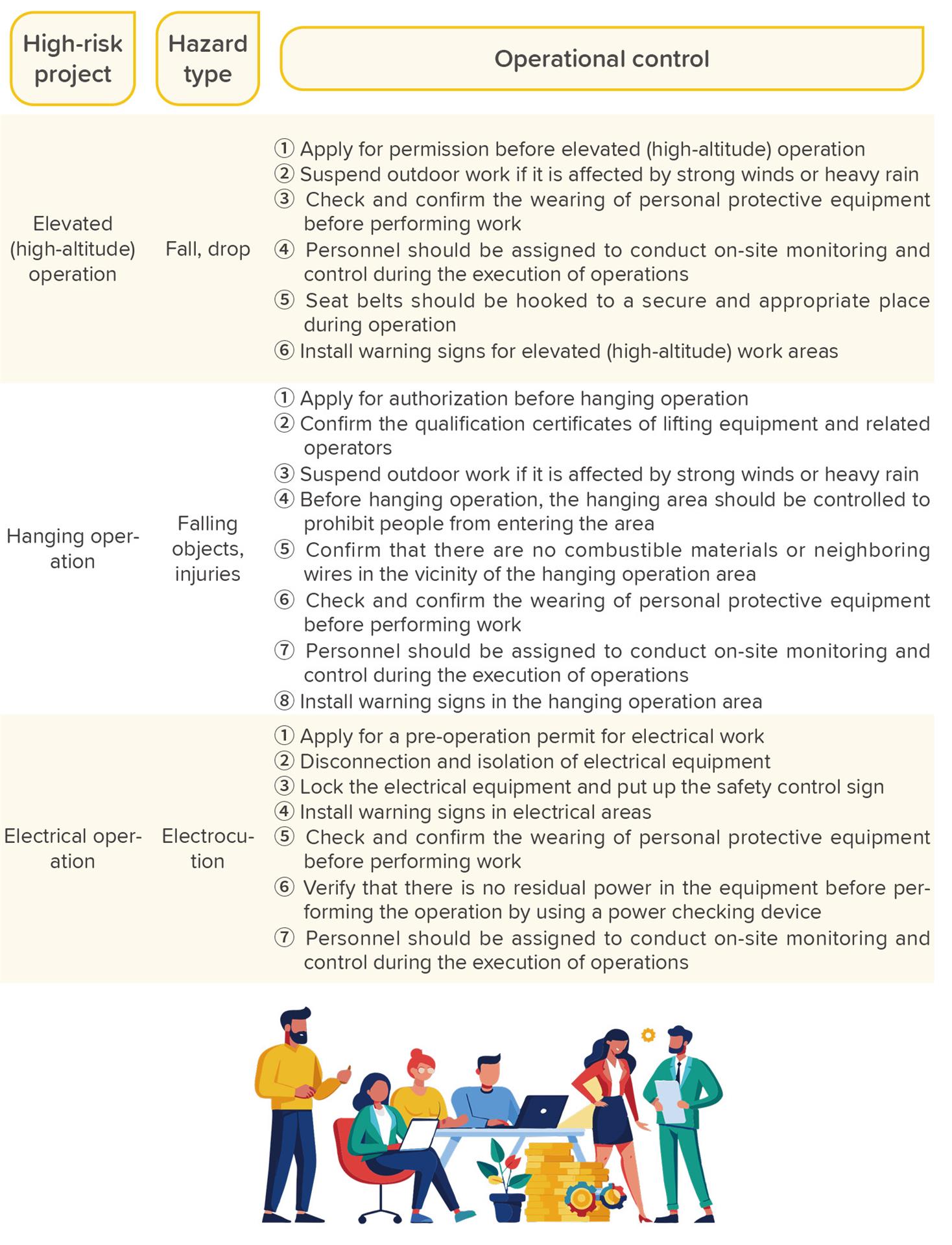
Operations safety control
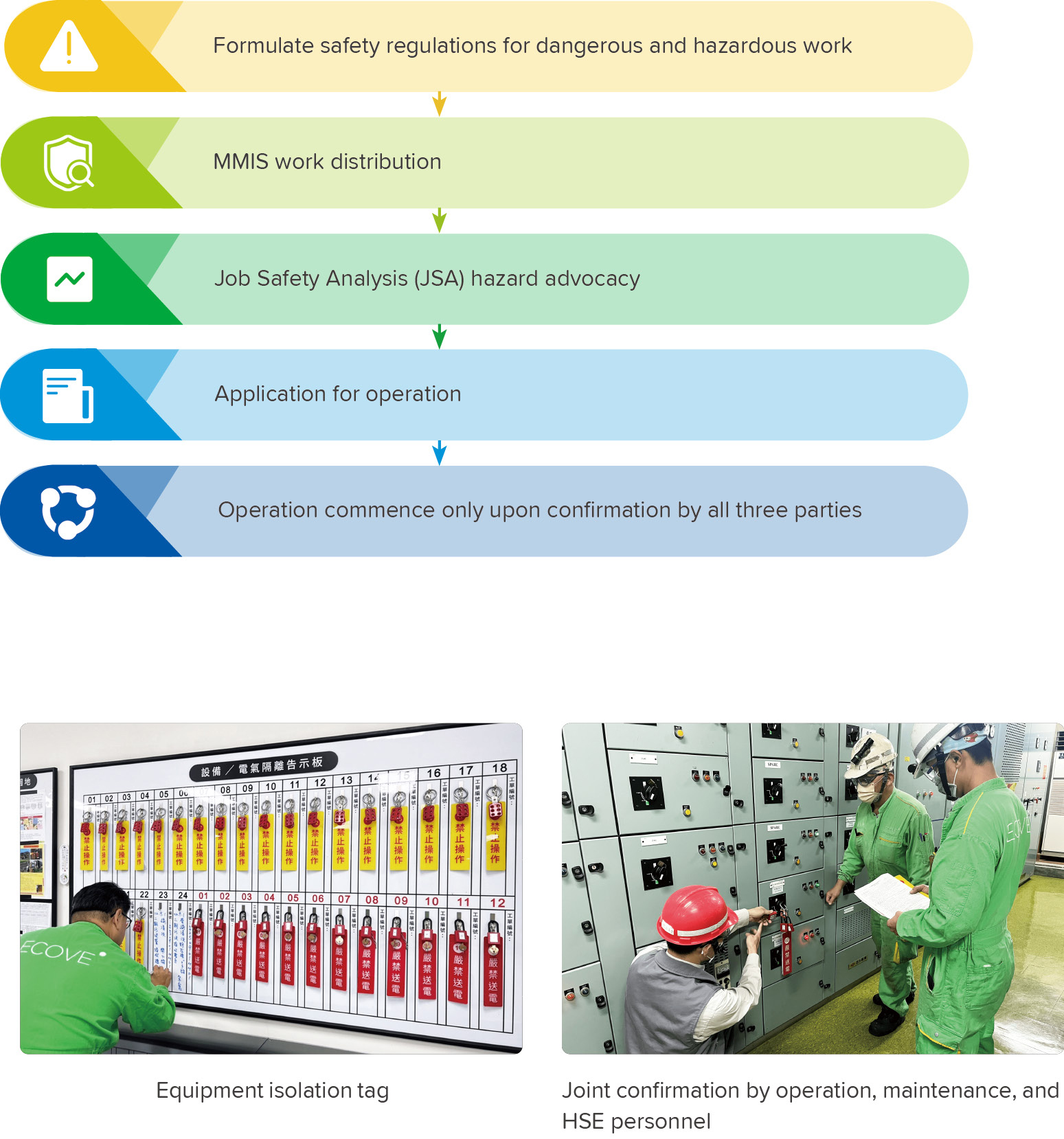
Mechanical Equipment Management and Contractor Management
Taking ECOVE Environment Service Corp. as an example, for the management of mechanical equipment, the MMIS system is utilized to schedule regular inspections of machinery and equipment in each operating management area, ensuring that maintenance planning and repair tracking are conducted through an electronic system to prevent oversights. Prior to operations, automated inspection plans are developed, including vehicle maintenance, and pre-operation checks are implemented. During operations, on-site observations and inspections are carried out, and post-operation site verifications are conducted, which are included in evaluations and reviews. Various safety control processes are implemented, supported by electronic systems for license and permit verification, ensuring the validity of certificates and confirming the qualifications of operators. This enables effective control of safety during operations. Before contracting a project, ECOVE Environment Service Corp. evaluates the safety and health regulations and hazardous factors associated with the project. This information is documented in the project procurement manual to facilitate the selection of suitable contractors. Annually, safety and health education and training sessions are conducted for contractors to enhance their awareness of safety and health practices. In accordance with the HSE policies and contract content, compliance with relevant OSH provisions shall be included (such as rights to withdraw laborers as per Article 18 Occupational Safety and Health Act). The training teaches workers how to protect themselves in unsafe or unhealthy situations.
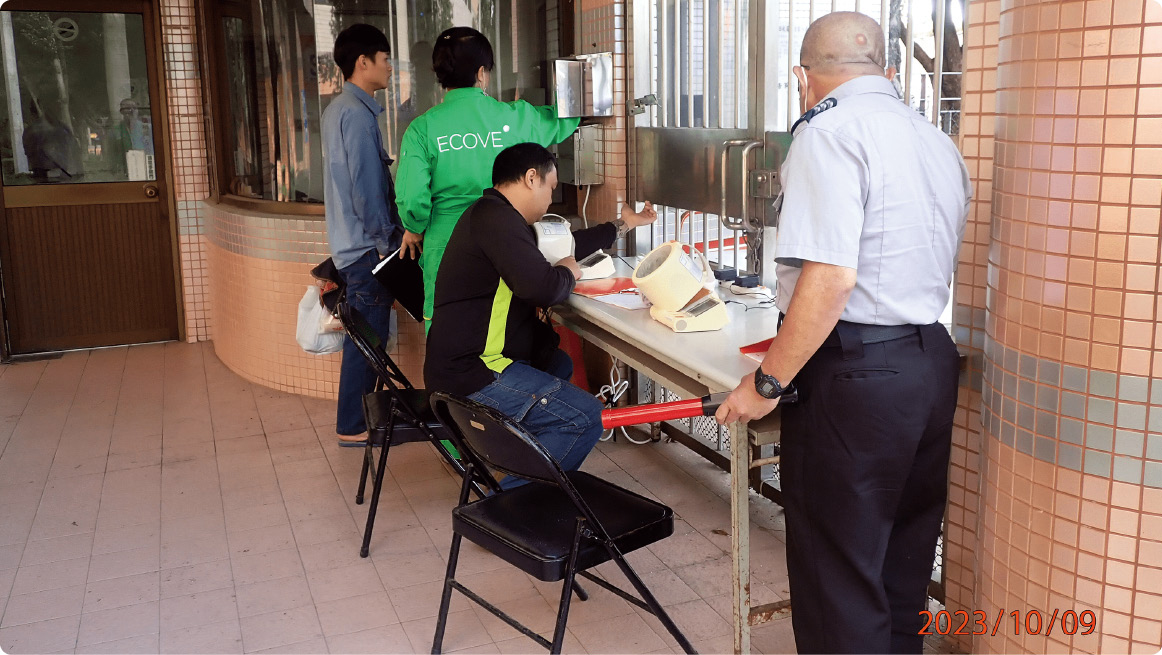
Contractor qualification control, unscheduled blood pressure measurement and alcohol testing through facial fingerprint recognition system
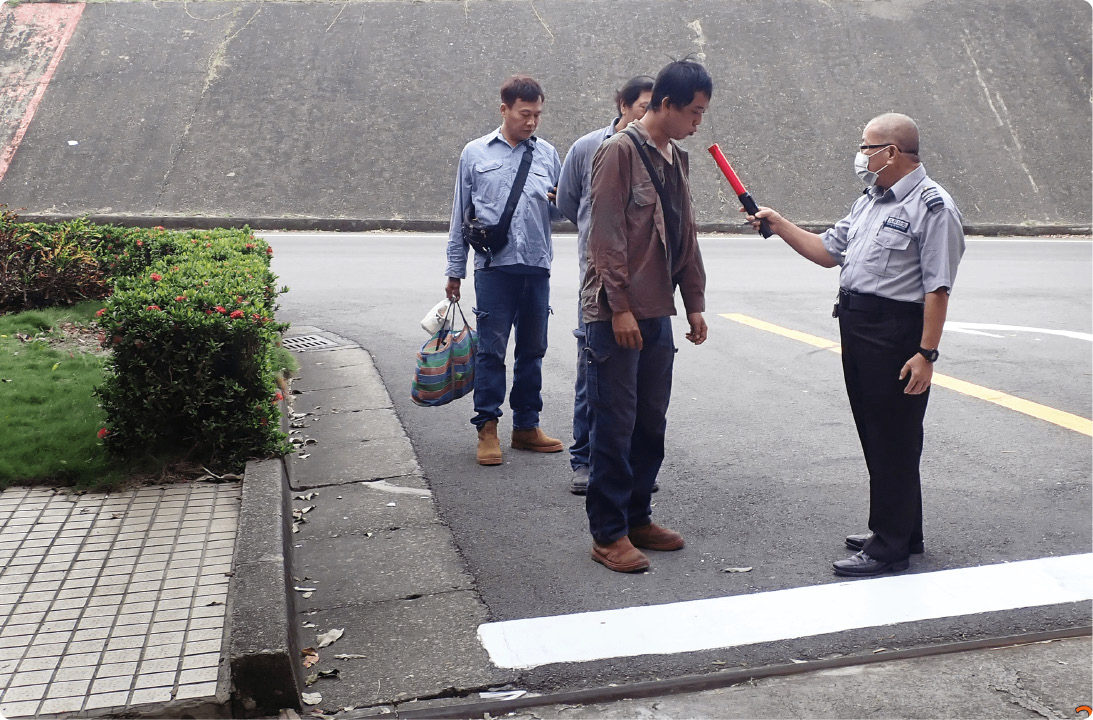
Contractor qualification control, unscheduled blood pressure measurement and alcohol testing through facial fingerprint recognition system
Prior to commencing operations, hazard notifications are provided, and meetings are organized to discuss and establish agreements. These measures aim to enhance safety and health awareness and consciousness during on-site operations. Additionally, all entering tools and equipment are inspected individually to ensure their safe use. During the construction period, toolbox meetings will be conducted on a daily basis while audits are conducted from time to time. Immediate rectification will be required whenever deficiencies are found, and review meetings will be held when necessary. After the completion of the work, the seven major occupational safety and health performance indicators will be evaluated to assess performance. These indicators are categorized into five levels: A, B, C, D, and E. Contractors with a D-level rating should be avoided, and those with an E-level rating will be included in the non-compliant vendor list. With regard to access control, besides utilizing facial and fingerprint identification systems for access control at each plant, qualification reviews for the construction personnel are also carried out. After permission has been granted, personal traits will be scanned into the identification system to reinforce access control for qualified personnel, and contractors will be included in the access control management. During the construction period, on top of the abovementioned audits and informative training, the Company will also run blood pressure or sobriety tests on the personnel from time to time. Should abnormalities be found, the work of the said personnel on that day will be stopped, so as to avoid any hazard of physical discomfort caused by constrained, working at heights or high temperature environment. Personnel is also constantly reminded to pay attention to the management of their own physical health and discipline. Regarding vehicle safety, safe driving, and hazardous substances, safety advocacy will be carried out during morning briefings through JSA. The personnel's health and fit to work will be assessed prior to the commencement of operations. If there are any unwell personnel, this shall be raised immediately and the person in charge shall make work adjustments immediately. Alcoholic beverages are strictly prohibited on-site and sobriety tests will be conducted as needed, and vehicle maintenance is managed according to the MMIS system. There was no traffic accident in 2023 for the cleaning and delivery fleet of ECOVE Waste Management Corp.
Reinforced Safety Management and Audit
To strengthen safety management, ECOVE gradually and continuously improves to achieve enhanced safety management through the auditing system. At the same time, employees' safety knowledge and competencies are also verified and confirmed via audit. Weaknesses are understood and incorporated into the training system and as a reference for amendments to the work standards. ECOVE Environment Service Corp. actively promoted a three-tiered audit management system whereby on-site engineers shall carry out the level 1 management of safety and health, OSH personnel and plant managers shall conduct the level 2 of safety and health audits (including the independent evaluation of each plant), and the Company conducts level 3 safety and health supervisory audits. Safety management and audit systems are realized through the merging of the audit system with assessments. The execution of third-level audits involves presenting reports on audit sessions and the number of deficiencies during committee meetings. The relevant departments under the management of each incineration plant and project are responsible for implementing improvements. The Company conducts follow-up audits to confirm the effectiveness of the improvements.
Three-tiered Audit Management
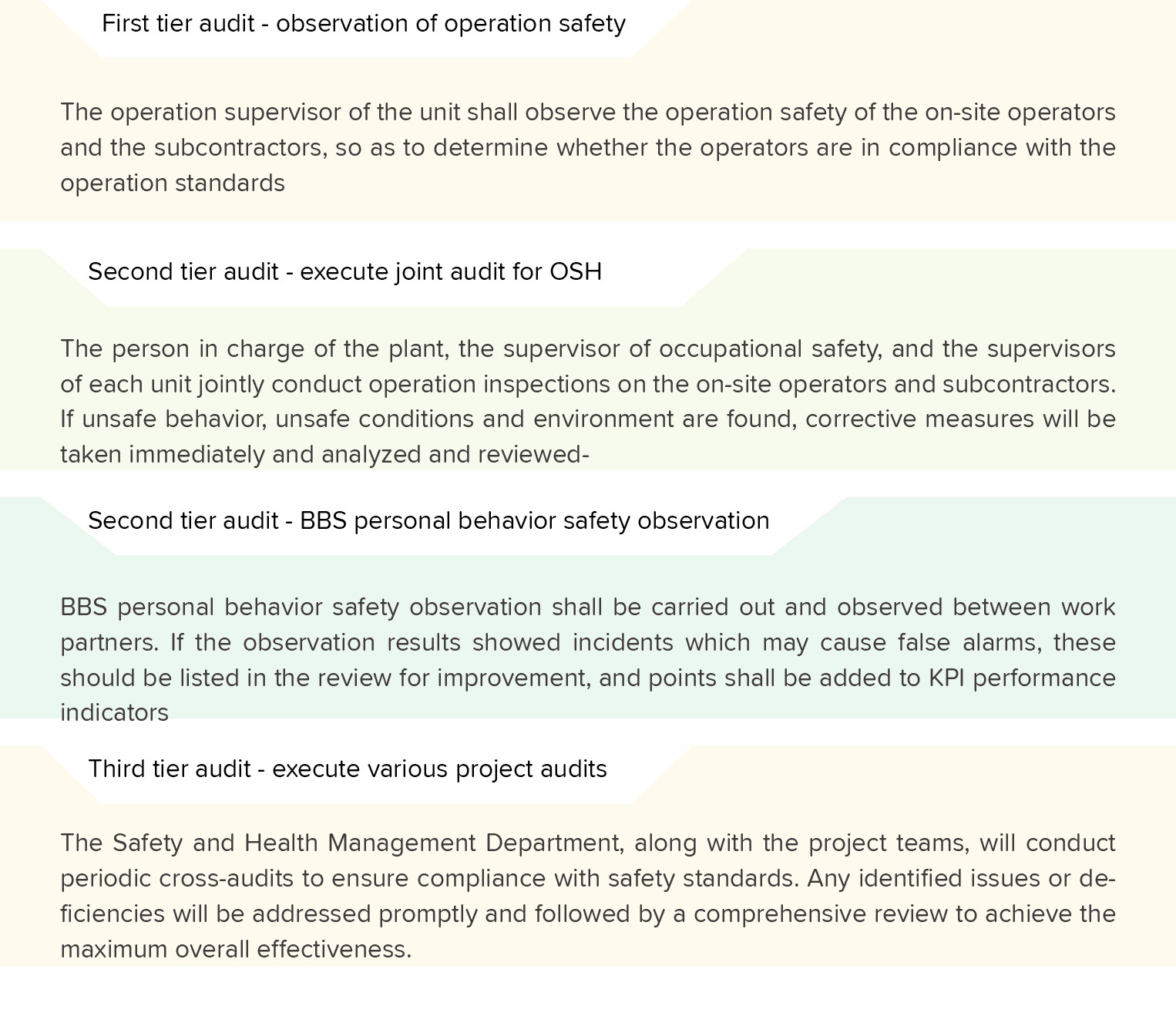
The Safety and Health Management Department requests the respective units under its jurisdiction to conduct root cause analysis for the identified audit deficiencies and develop corresponding improvement measures. Once the solutions are determined, corrective actions are implemented. The Safety and Health Management Department provides feedback to the relevant departments (Operations Department 1, Operations Department 2, or Project Department) and informs them of the corrective actions taken. The improvement results are presented and closed during company senior meetings. Audit not only includes internal head office inspection or project cross audit, but also regular or irregular audits conducted by local external competent authorities in accordance with the annual inspection policy. Post audit, the local project will be informed of the inspection results immediately, and the local project shall be requested to cooperate in the implementation of safety management.
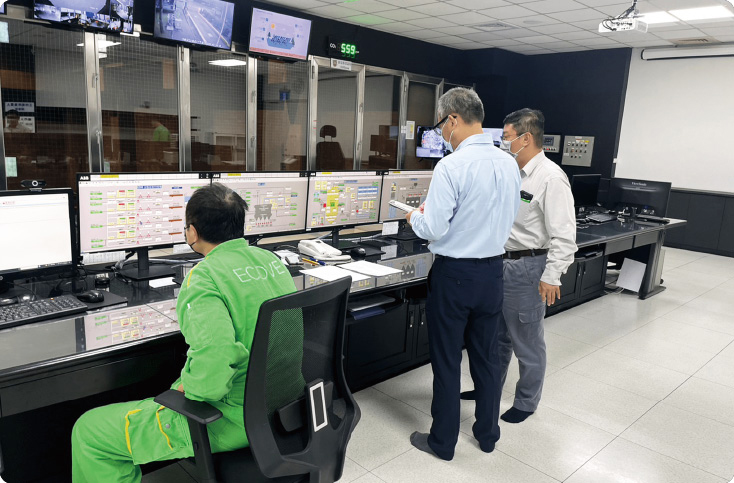
ISO 45001 external audit on-site inspection
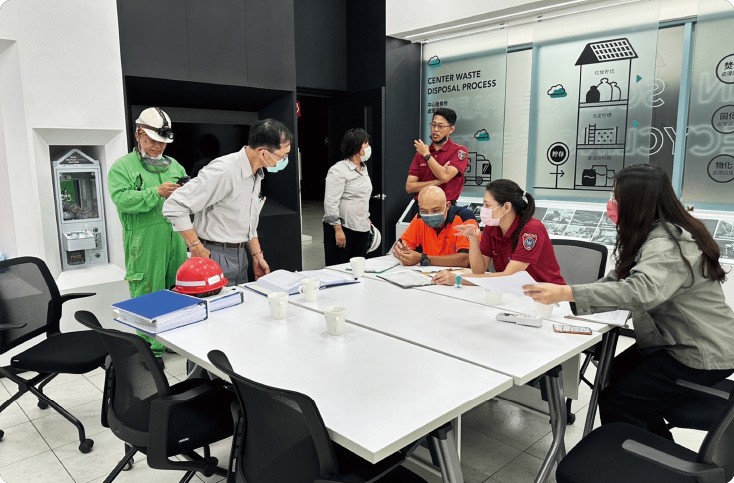
Fire brigade supervising inspection operations
Occupational Disaster Prevention
ECOVE has always attached great importance to workplace safety and health, and has actively invested in relevant resources, including proper risk identification and assessment, education and training, work safety control procedures, emergency response drills, and occupational disaster investigation mechanism. ECOVE has invested resources to provide a safer working environment for our staff and to make each and every one of them realize that safety is closely related to the individual. ECOVE and all staff members are fully committed to the implementation of safety and health management, and consider disaster-free as the first and foremost priority of our safety operations. Through the implementation of various programs and systems, and adhering to the core value of "people-oriented", ECOVE has invested in manpower and resources for the safety and health maintenance of our staff to create a safe and healthy working environment, and we will do our utmost to create disaster-free working hours with the concept of sustainable management.
Occupational Accident Incident Investigation Mechanism Flowchart
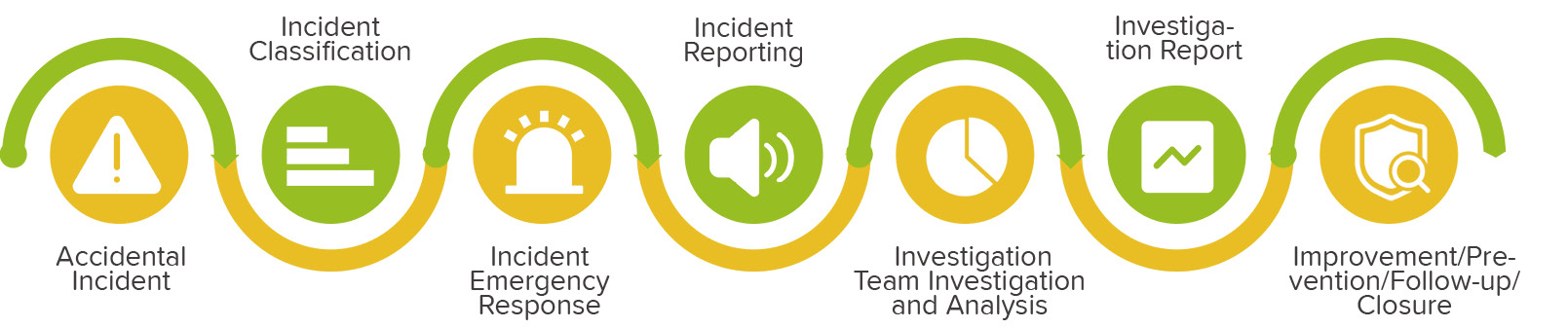
Providing a safe and secure working environment for our colleagues is a top priority for ECOVE and its subsidiaries, and we have invested in building a friendly, healthy and safe workplace. At ECOVE, "safety first" is neither a slogan we merely pay lip service to nor is it a routine matter. It is fully internalized as the daily work practices of all personnel. For safety issues, in addition to general safety and health education and training, special operation hazard education and training (confined space operation, elevated (high-altitude) operation, hot work operation, hanging operation, electrical operation, rotating equipment operation, piping repair operation, etc.), hazard education and training, contractor safety and health education and training, and emergency response drills, etc., we have provided perfect training to enable our employees to complete their work on time and in good quality. In addition, on various occasions, our supervisors have been reminding our employees that safety should not be compromised, and we have also deepened our employees' awareness of safety through their sharing of safety quotes.
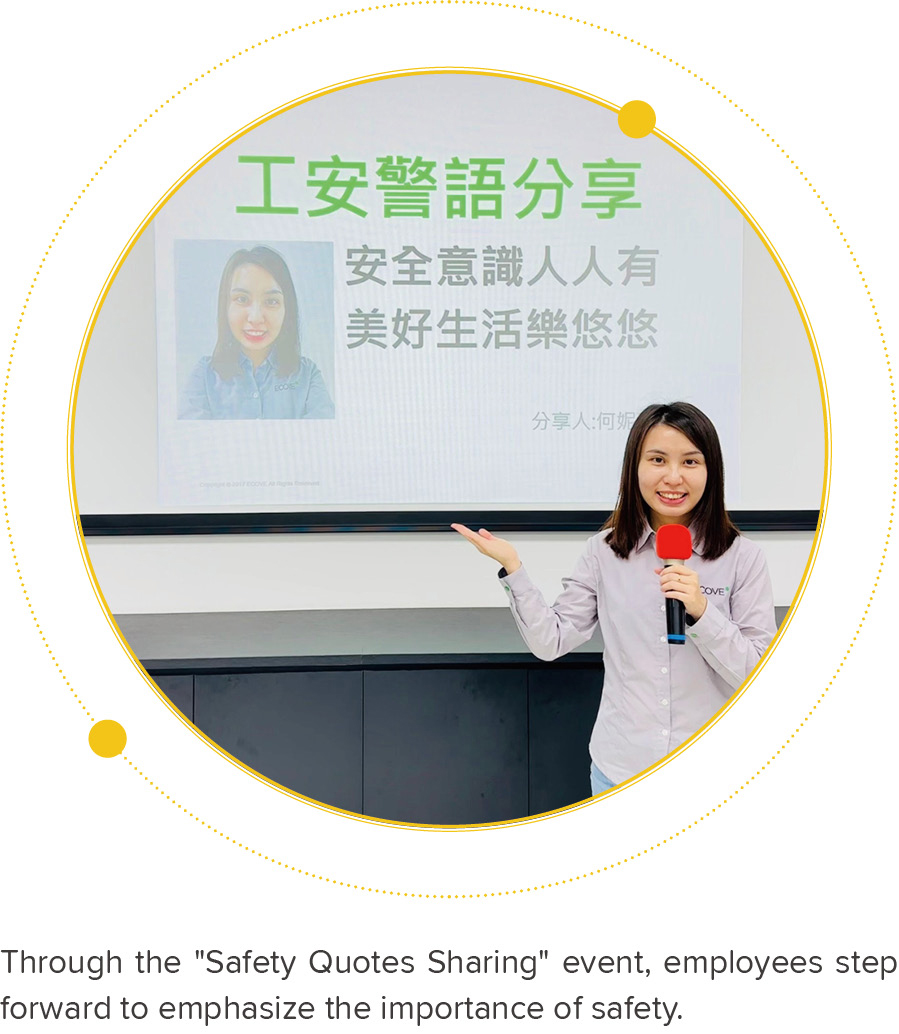
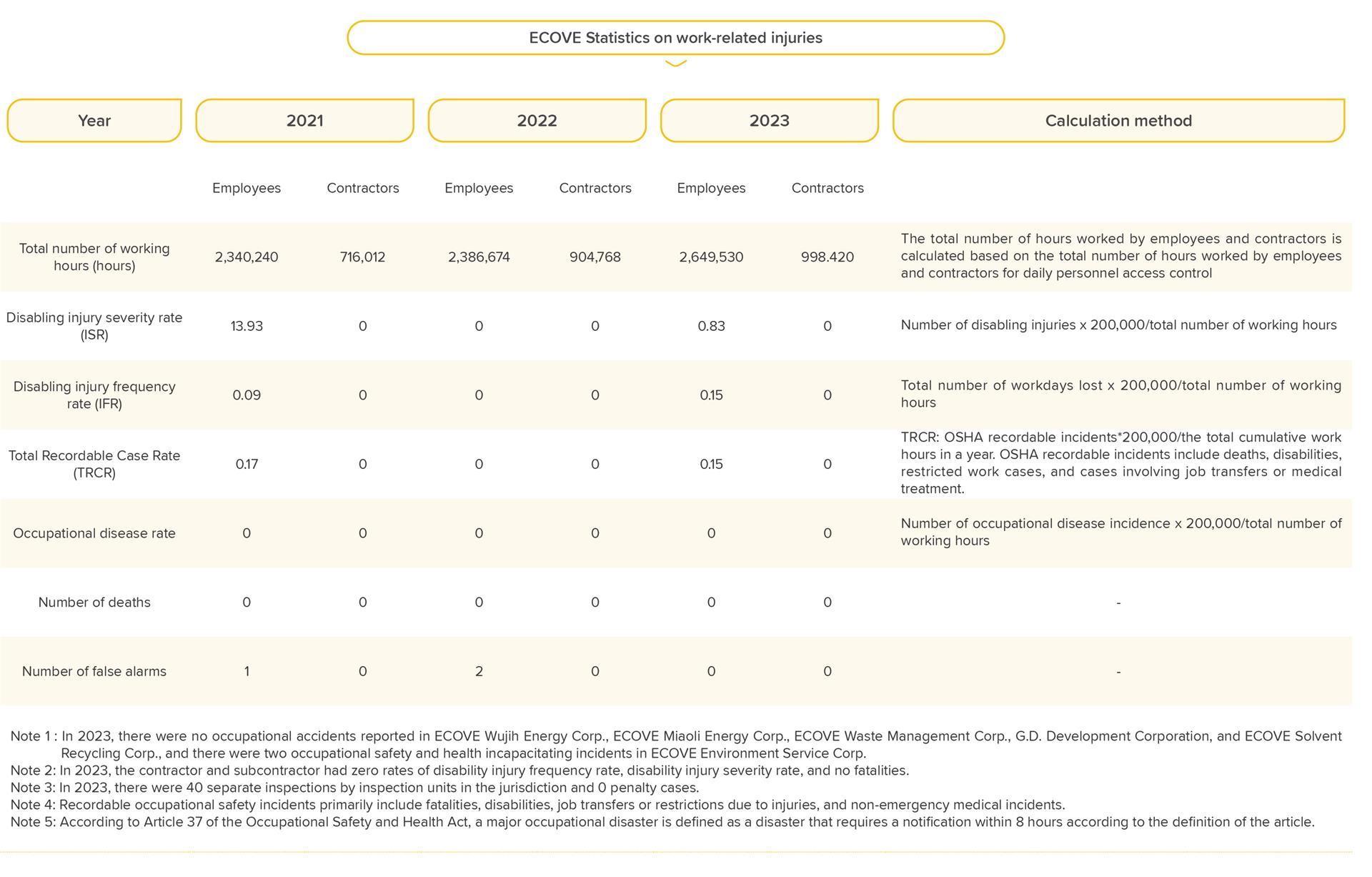
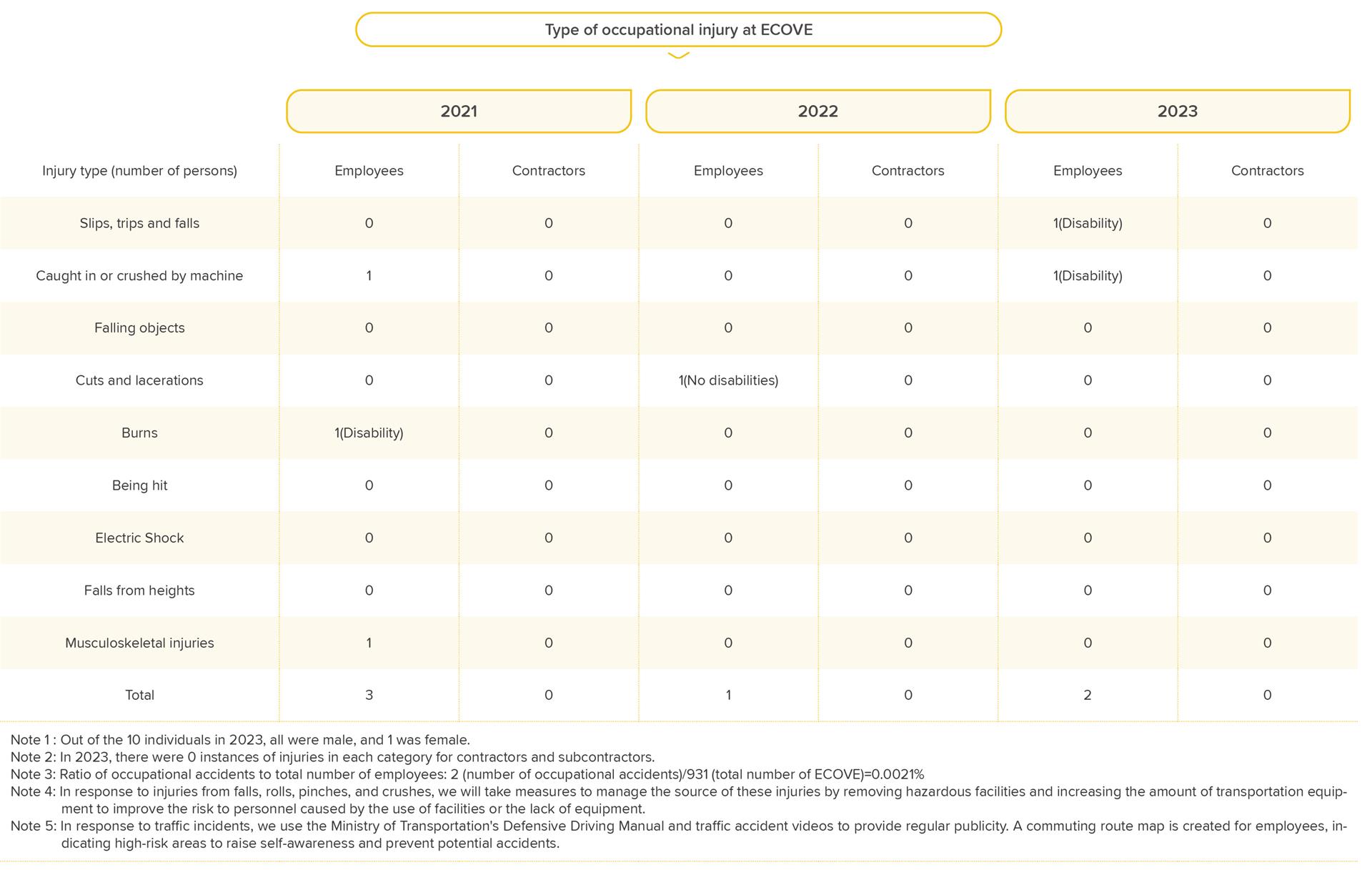
Obtaining ISO 45001 Certification
ECOVE upholds the spirit of prioritizing safety, health, and the environment, following the seven major HSE policies. Its subsidiary, ECOVE Environment Service Corp., and all 10 operational waste incineration plants have obtained OHSAS 18001 and TOSHMS certifications since 2009. In 2011, in response to the Ministry of Labor's policy, TOSHMS was fully converted to CNS 15506, and continuous verification has been maintained. Starting from 2018, all 10 operational sites of ECOVE Environment Service Corp., ECOVE Waste Management Corp., ECOVE Solar Energy Corp., and ECOVE Solvent Recycling Corp. have successively obtained ISO 45001 certification, and the occupational safety and health management system, internal audit, and certification coverage rate of each operation site is 100%. The certification includes all workers in the workplace, including employees, contractors, and subcontractors. In 2019, all locations, including the headquarters, under ECOVE successfully completed inspections, and ECOVE Environment Service Corp., ECOVE Waste Management Corp., ECOVE Solar Energy Corp., and ECOVE Solvent Recycling Corp. have maintained the validity of their certifications in 2023.(Note)
Note:There are 10 operating locations including the headquarter (ECOVE), Keelung, Taoyuan South, Miaoli, Houli, Wurih, Xizhou, Tainan, Tainan Science Park, and Gangshan. ECOVE Wujih Energy Corp. and ECOVE Miaoli Energy Corp. do not meet the setup standards, but they are located within validated operating locations. The headquarter (ECOVE) is located in the same building as ECOVE Environment Service Corp., ECOVE Wujih Energy Corp. is located in ECOVE Environment Service Corp.'s Wurih plant, and ECOVE Miaoli Energy Corp. is located in ECOVE Environment Service Corp.'s Miaoli plant. All employees and non-employees, etc. are covered by the Occupational Safety and Health Management System.
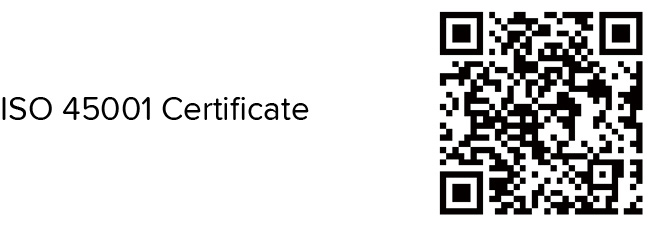
Awards
In order to actively promote the development of a safety and health culture and to strengthen the autonomy of safety and health management, ECOVE encourages all units to participate in external safety and health competitions, which have won many awards, demonstrating the effectiveness of our safety and health promotion efforts. The awards received by ECOVE and its subsidiaries in 2023 are listed below:
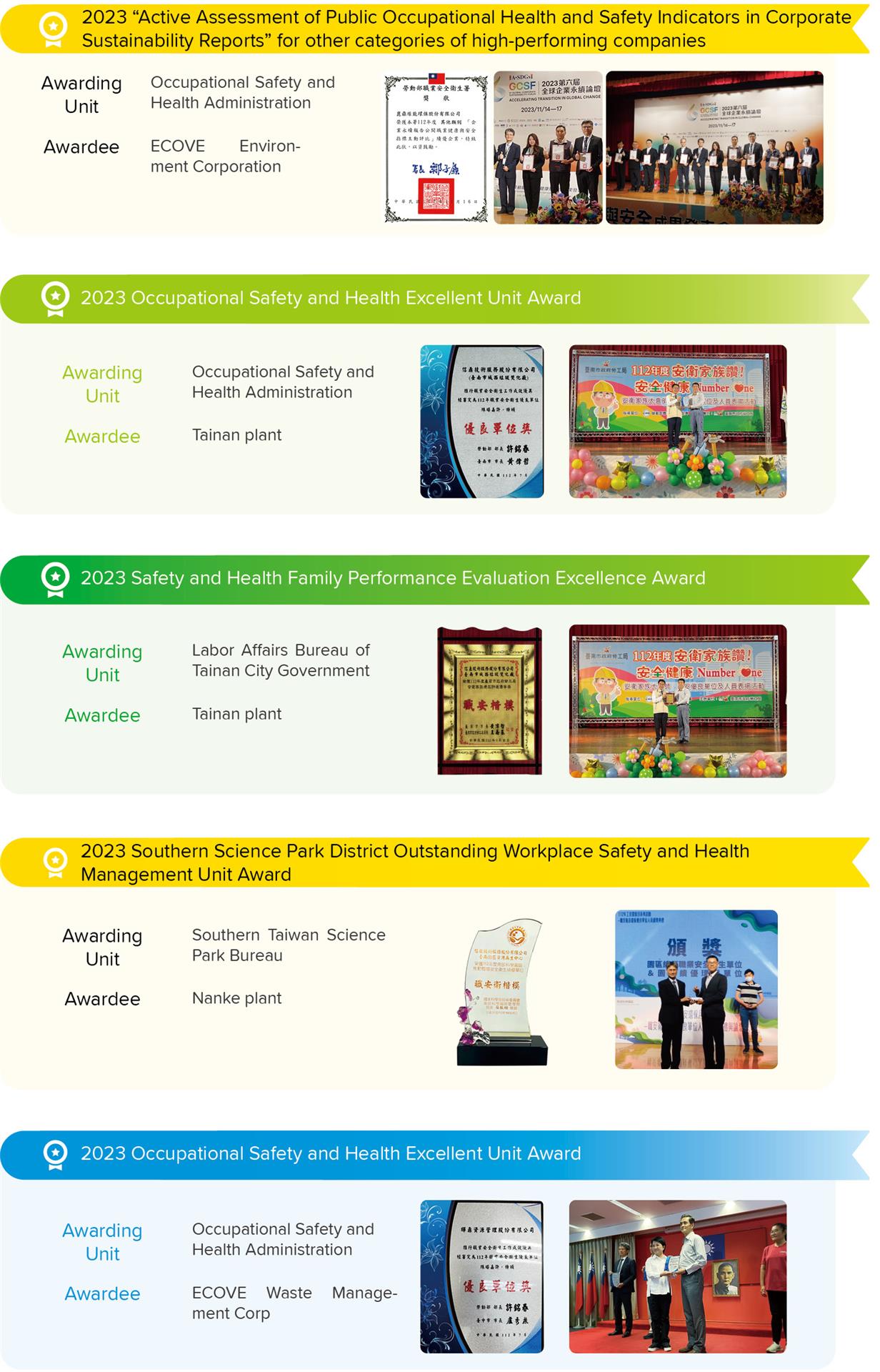
Workplace Health Management
Considering the working environment and conditions of the employees, ECOVE has planned a comprehensive health management system to provide each new employee with a general physical examination, the frequency of the general health examination of in-service employees once every two years, which is better than the legal requirements. In addition, according to ECOVE Environment Service Corp.'s proprietary monitoring and comparison of employee working conditions and possible hazardous exposures, special health checkups are conducted for employees who may be exposed to hazards, e.g., special health checkups for dusty work are conducted once a year. Regular occupational and environmental monitoring is conducted to ensure effective management of the work environment and employee health. Currently, the implementation of health examinations is in good condition, with no reported occupational disease-related deaths or confirmed cases of occupational diseases diagnosed by specialist occupational physicians in the past 24 years. In the occupational health service aspect, we assess the potential hazards that employees may be exposed to in the work environment. We organize relevant educational training sessions and provide consultations to ensure that employees have a comprehensive understanding of their work environment and are equipped with the knowledge to protect their own health and minimize health impacts. In 2023, a total of 14 health education lectures were conducted, with a total of 313 participants. In addition, its subsidiaries - ECOVE Environment Service Corp. regularly performs on-site services through full-time nurse practitioners and occupational specialists, while ECOVE Waste Management Corp. provides on-site services through a contracted company due to the fact that it has more than 50 employees. The remaining subsidiaries with fewer than 50 employees have all been merged into the headquarters or ECOVE Environment Service Corp.'s health care services for free medical consultation and health guidance for employees, which facilitates the understanding of employees' physical or mental health problems and promotes employees' awareness of health management and their ability to take action. In 2023, a total of 44 hours were dedicated to on-site services, covering 15 sessions. Although the abnormality rate in health check results may be influenced by factors such as age, personal lifestyle habits, and other objective factors, we still prioritize providing enhanced health promotion guidance to employees with higher abnormality rates. We have developed an annual health promotion plan to implement various health promotion initiatives accordingly. In addition, on-site service physicians and nursing staff conduct on-site hazard assessment, health examination abnormality tracking, general health examination consultation, chronic disease tracking and injury tracking, and organize related health promotion activities in line with annual health examination abnormality trends and epidemics, such as: “If you eat right, your blood glucose will not go out of control” and “Reducing oils, reducing stress, and becoming healthier” seminars to enable employees to understand their personal health situation, which include personal health examination values related to metabolic syndrome and health education information on staying away from metabolic syndrome. Through the organization of the health promotion activity “Stress reduction starts from the heart”, the Company announced the EAP (Employee Assistance Program) related resources for colleagues to understand and provided articles on stress reduction and hygiene education on the Company's internal platform for colleagues' reference, as well as organized the related essential oil stress relieving courses for colleagues to participate in. In order to take care of the health of colleagues, CTCI has set up a health care system platform to provide health news, health check hospital appointments, health questionnaire filling, health promotion activities and health care consultation registration, etc. It also strives to promote the intelligent systematic Hygeia health management system, which collects and analyzes data, and makes effective use of the systematic system to grasp the health information of the employees and report statistics for risk management. With a multifaceted approach to health management, general health check-ups and management are categorized into four levels: normal, mild, moderate, and severe abnormalities. The percentage of health check abnormality in 2023 was 22%. They are prioritized as the primary monitoring targets, and relevant health education and follow-up are provided to them. If necessary, medical treatment and medication are recommended to ensure a comprehensive understanding of the current physical condition of employees. This is a primary task for healthcare professionals. For employees without levels 3 and 4 abnormalities in special health check-ups, we will continue to adhere to protective measures and conduct regular monitoring to safeguard their health and prevent occupational diseases. In 2023, we focused on preventing diseases related to excessive workloads. We provided personal health guidance to 98 individuals with moderate to high abnormals, conducted follow-ups for 200 individuals with abnormal health check results, and had physician consultations with a total of 98 individuals, achieving a completion rate of 100%. In 2023, we provided maternal health protection for 2 individuals in the workplace, and all cases were successfully closed within the year. In our commitment to corporate health and sustainability, we recognize the importance of managing the health of our contractors. We are committed to working with our contractors to ensure that their work environment and the health of their employees are given proper attention and support. Our contractor health management includes the following elements: training and education: we implement daily toolbox meetings to provide information on relevant hazards, so that our contractors understand and comply with health and safety standards and promote a healthy culture in the workplace; health monitoring and tracking: we require our contractors to ensure that they have established health monitoring and regularly track the health status of their employees and identify and respond to health problems in a timely manner; emergency response plan: we develop and implement an emergency response plan in conjunction with our contractors to respond to potential health emergencies; communication and feedback mechanism: we have established an effective communication and feedback mechanism to enable timely sharing of information and resolution of problems between our contractors and us, and to ensure the effective implementation of health management. Through these measures, we are committed to working with our contractors to maintain a safe, healthy and sustainable working environment. In addition, we have made adjustments to our employee care and welfare measures for this year and next year. We will continue to uphold the principle of taking care of our colleagues, so that they can learn and grow together in the ECOVE family without worrying about their future. Regarding employee health checkups, the annual subsidy amount will be increased from 2024 onwards, and adjusted to increase the subsidy amount as the age of colleagues increases, taking into account the needs of different age groups, as shown in the table below.
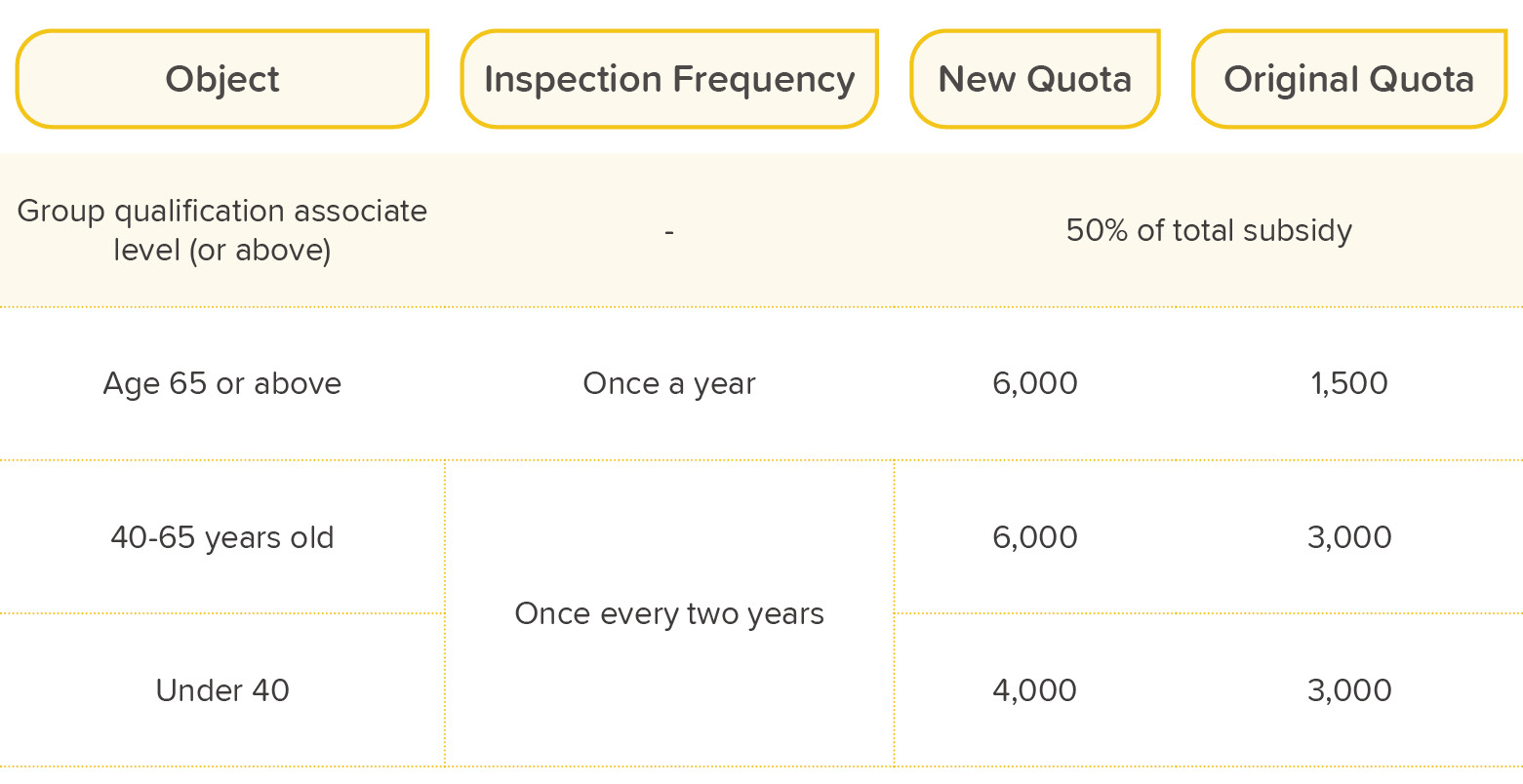
Health Management and Seminars
ECOVE and its subsidiaries provide occupational health services and promotion activities
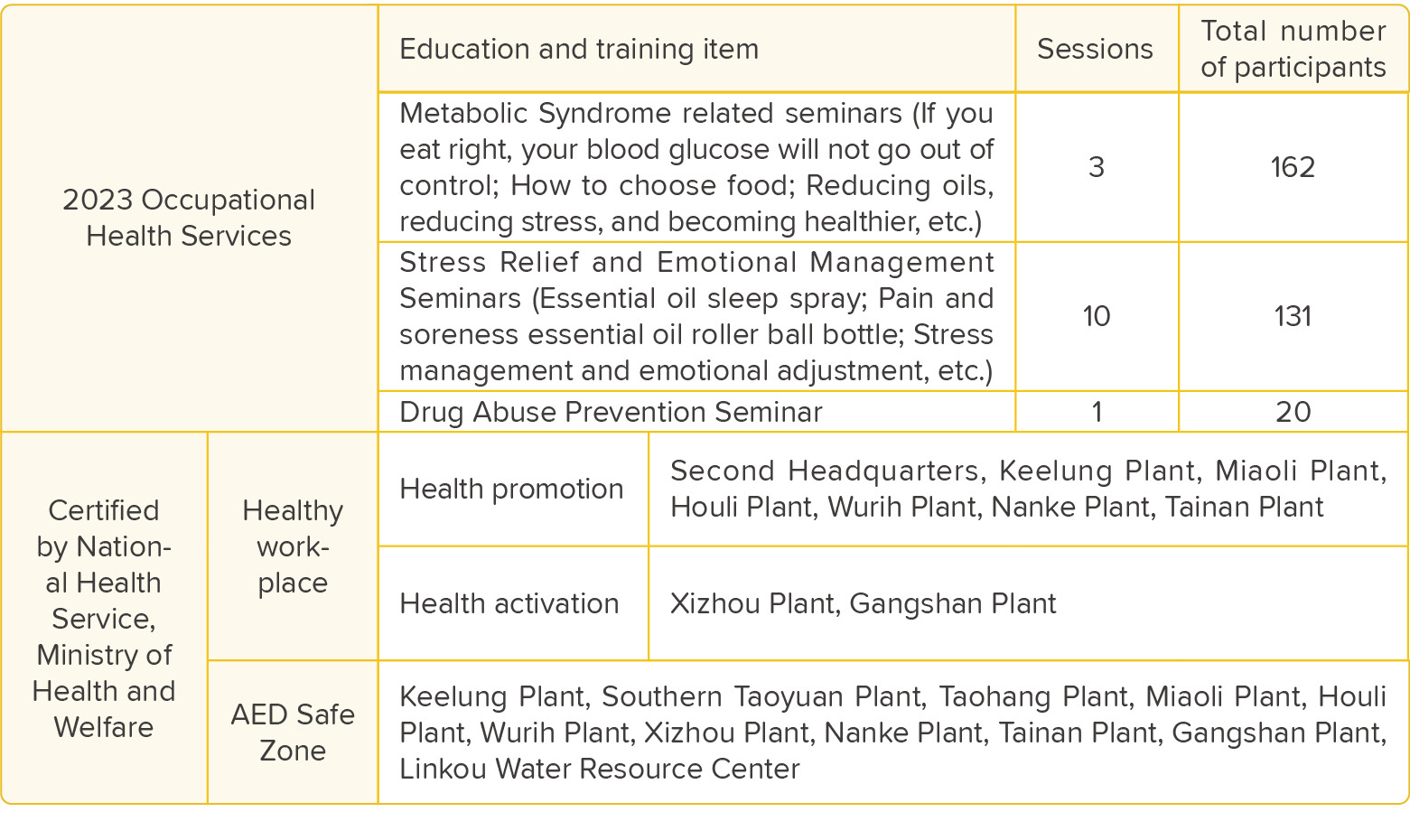
Health Lecture-Related Photographs
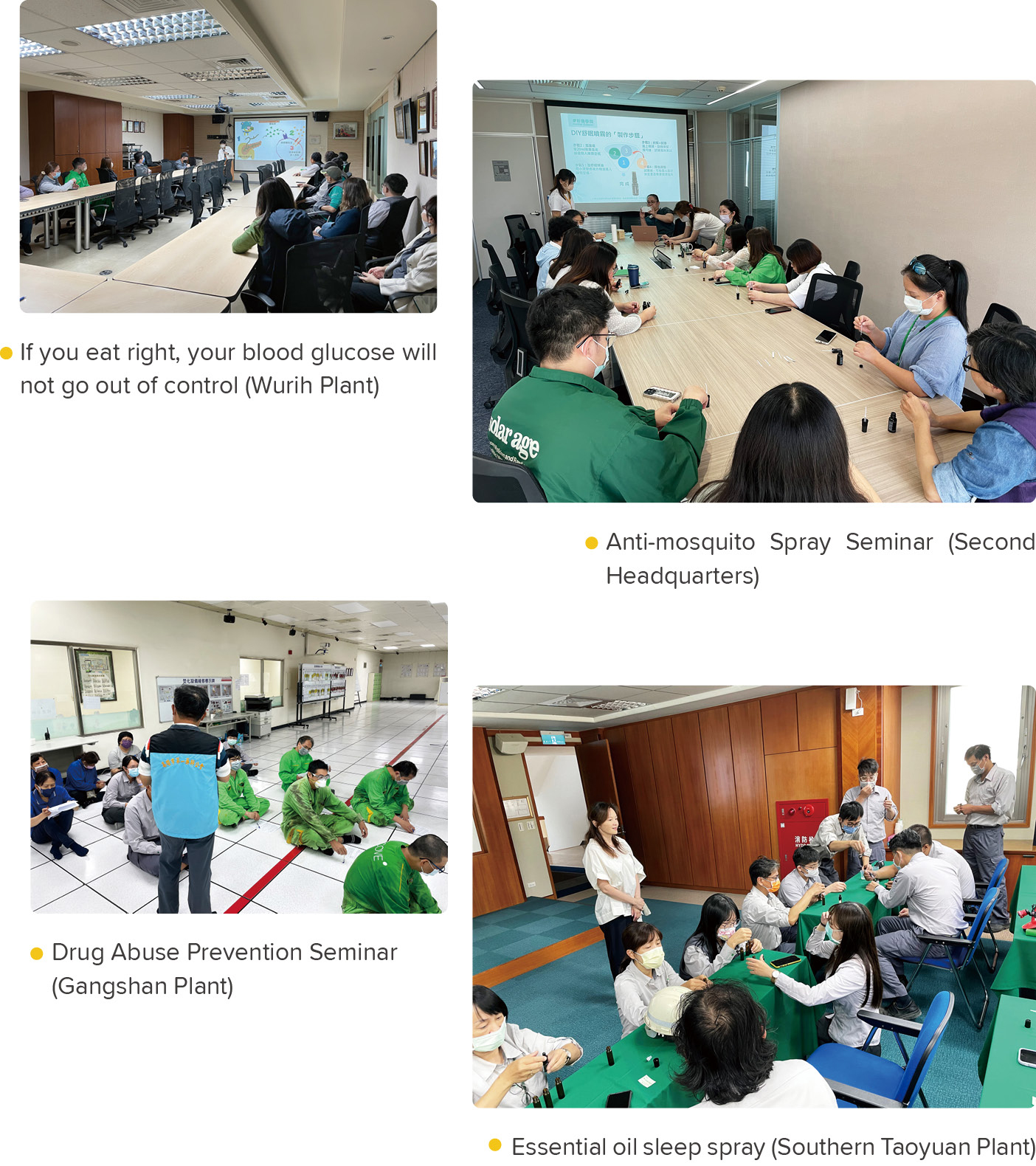
Health Promotion Activities_Substance Abuse Painting Exhibition (Come! I have something to tell you)
Through the cooperation with the National Museum of Natural Science in Taiwan, a special exhibition on drug abuse was held at the Miaoli, Tainan, and Gangshan factories alternately. The exhibition is oriented towards the characters in famous paintings such as Mona Lisa, the girl with pearl earrings, the Son of Man, Pandora, the sad old man, and Venus in the mirror, whose faces and states change when they are exposed to drugs, so that colleagues can see the horror of drug addiction through the comparison of the paintings, learn about the mechanism of drug addiction, and about the hazards and pitfalls of various types of drugs, as well as learn from them about drugs in order to avoid being exposed to them and falling into the abyss of drug addiction.
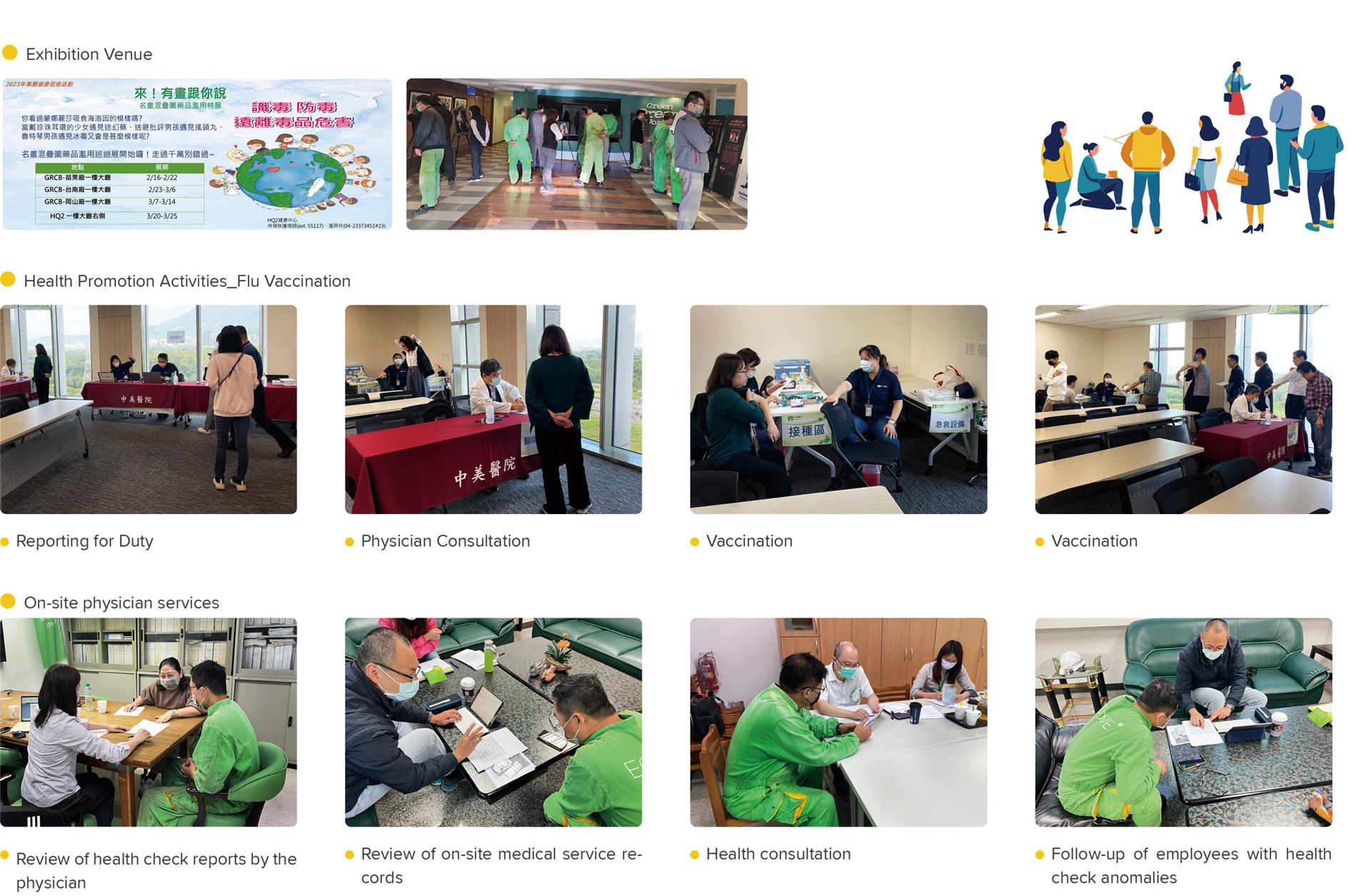
Dioxin tracking test
In addition to creating a safe working environment, we are committed to ensuring the health of our employees. Since 2008, we have entrusted the Research Center of Environmental Trace Toxic Substances of National Cheng Kung University to conduct analyses based on job nature, exposure environment, and years of service. Following the age-service operation interval and regulations for dust exposure in the workplace, representative employees from each operational area are selected for blood dioxin testing and monitoring. This blood test and follow-up examination are conducted every 4 years, and we have completed four consecutive rounds of testing to date. Additionally, we conduct health, dietary, and occupational exposure assessment questionnaires for cross-referencing purposes. The results show that the blood dioxin levels of the tested employees are relatively low compared to the general population in Taiwan and the recommended blood dioxin concentration values by the World Health Organization (WHO). This is because ECOVE's incineration plant has a comprehensive and effective air pollution control mechanism. Additionally, the Company has implemented education and training programs to enhance employee health and safety awareness, leading to an increased usage of personal protective equipment. This achievement not only makes ECOVE the first of its kind in Taiwan but also sets a benchmark globally. The next inspection is scheduled to take place in 2024. The Company takes a rigorous approach to addressing the hazards of dioxin. Since dioxin accumulation is primarily related to ingestion, reducing exposure and modifying eating behaviors can significantly decrease dioxin accumulation. To prevent employees from being exposed to dioxin in the workplace, regular safety and hygiene education training is conducted before the annual maintenance operations. Employees are taught how to correctly wear personal protective equipment and strict safety controls are implemented during operations. Random checks are conducted to ensure compliance with PPE usage and safety protocols, and supervisors and managers perform regular inspections. If any employee is found to be not wearing the required protective equipment or if safety protocols are not being followed, they are immediately instructed to stop the operation until proper protective equipment is worn, and safety measures are in place. This requirement not only emphasizes safety but also demonstrates our commitment to our employees and their families, ensuring that they can leave for work happily and return home safely. It is not just a slogan, but a tangible action we take.
Photos of dioxin testing at National Cheng Kung University
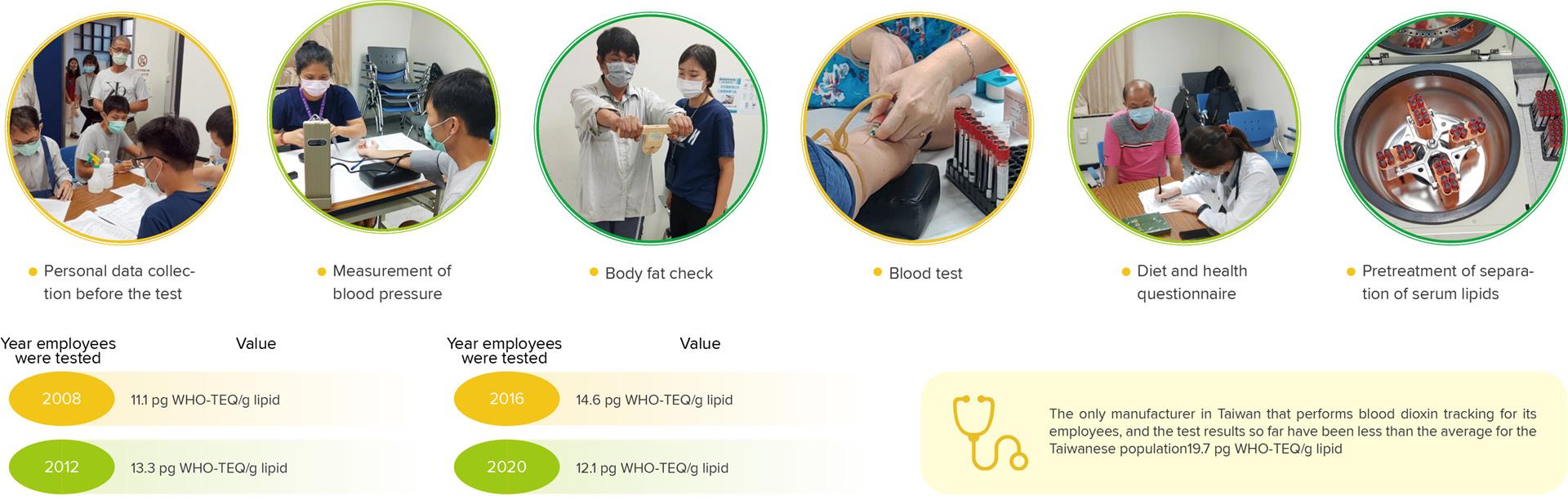
In 2020, a total of 38 urban solid waste incinerator operators were tested, and the average blood concentration of polychlorinated dibenzo-p-dioxins/furans (PCDD/F) was found to be 12.1 pg WHO9 8-TEQ/g lipid. This value is lower than the average test result in 2016 (14.6 pg WHO9 8 -TEQ/g lipid) and 2012 (13.3 pg WHO9 8 -TEQ/g lipid), but slightly higher than the average test result in 2008 (11.1 pg WHO9 8 -TEQ/g lipid). The results indicate that despite long-term exposure to the incinerator work environment, the blood concentrations of polychlorinated dibenzo-p-dioxins/furans (PCDD/F) in the 38 urban solid waste incinerator operators did not show a significant increase.
HSE Series Activities
The HSE Series Activities are organized annually. In 2023, through the Safety Open Letter from the General Manager of ECOVE, all employees were reminded of the importance of building a safety consensus, understanding potential hazards, and implementing safety measures. Various levels of supervisors provided on-site guidance and inspections to ensure compliance with work safety requirements. Emergency response training was conducted through hands-on exercises, allowing employees to immerse themselves in realistic scenarios and understand how to respond effectively in such situations. Contract management also continuously engages in safety reflection, proposing innovative ideas or improvement suggestions to achieve the implementation of safety and health measures.
HSE Open Letter
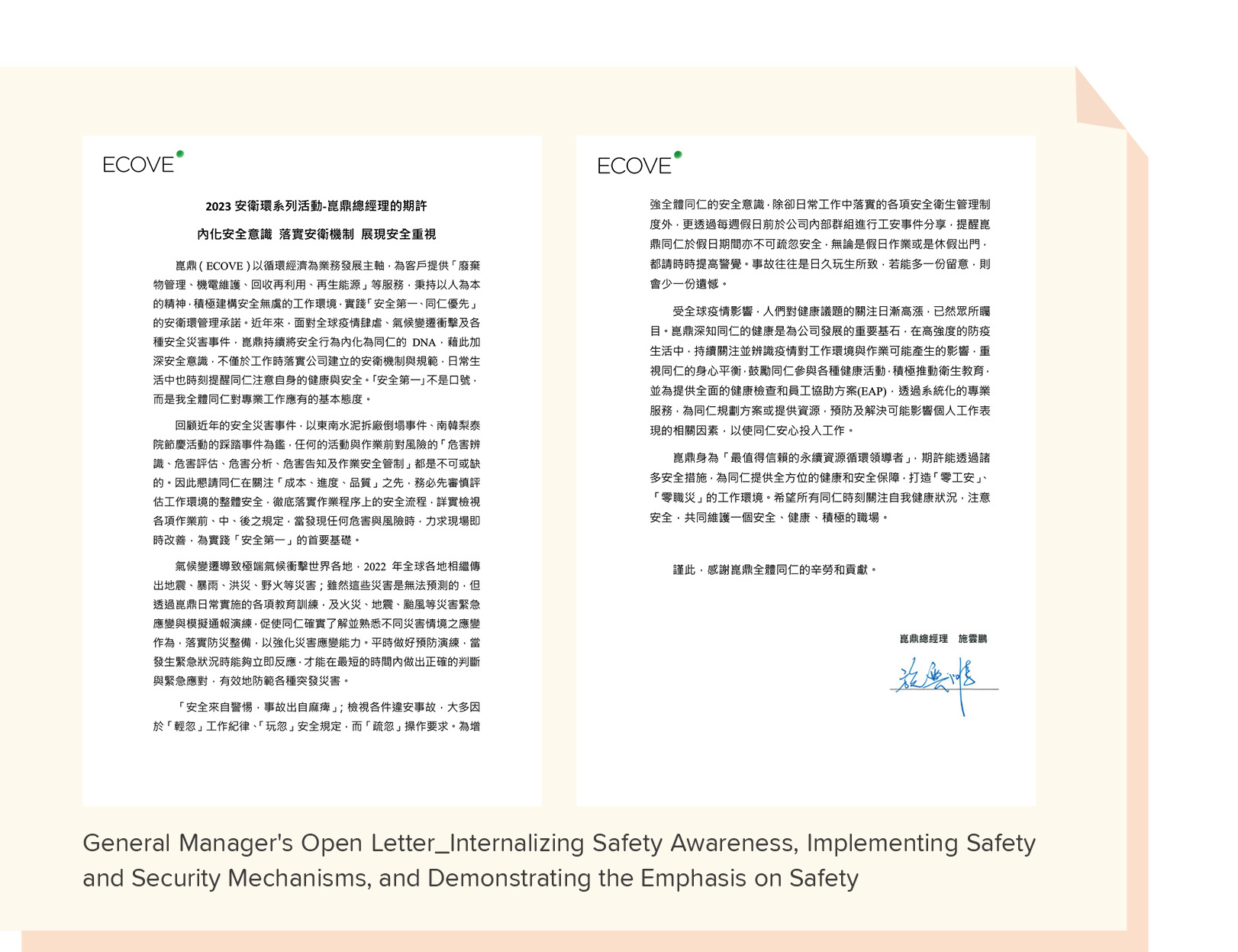
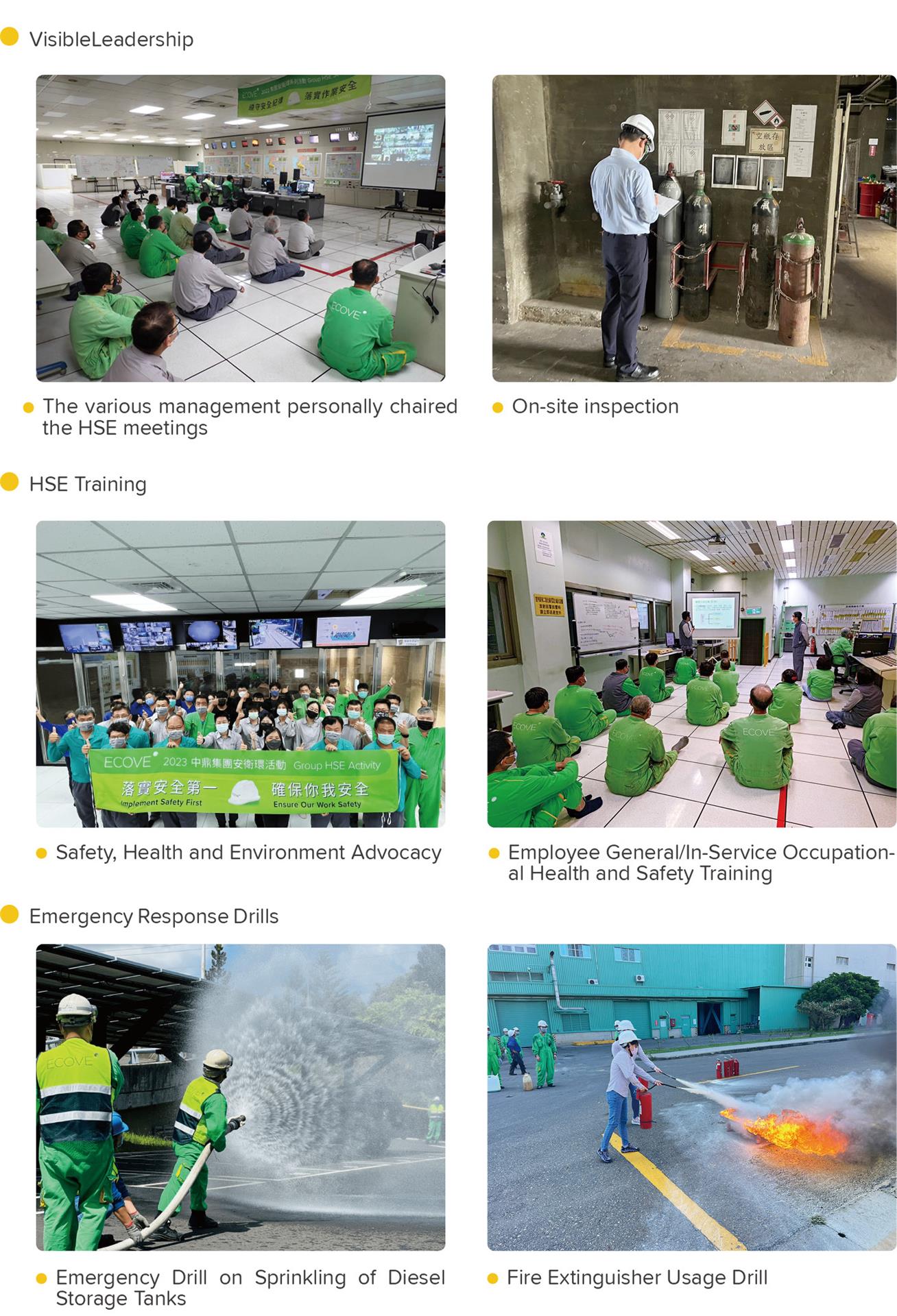
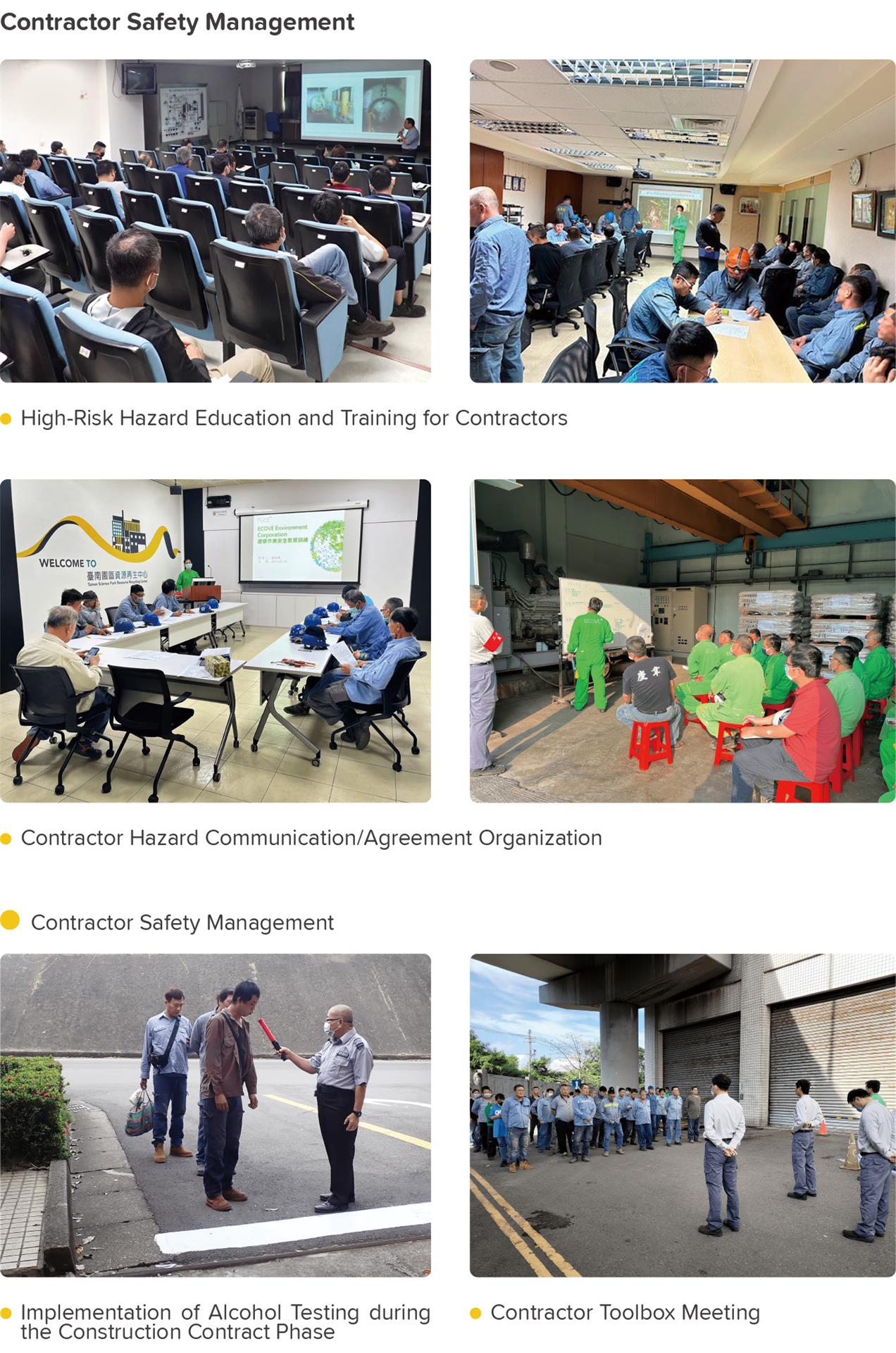
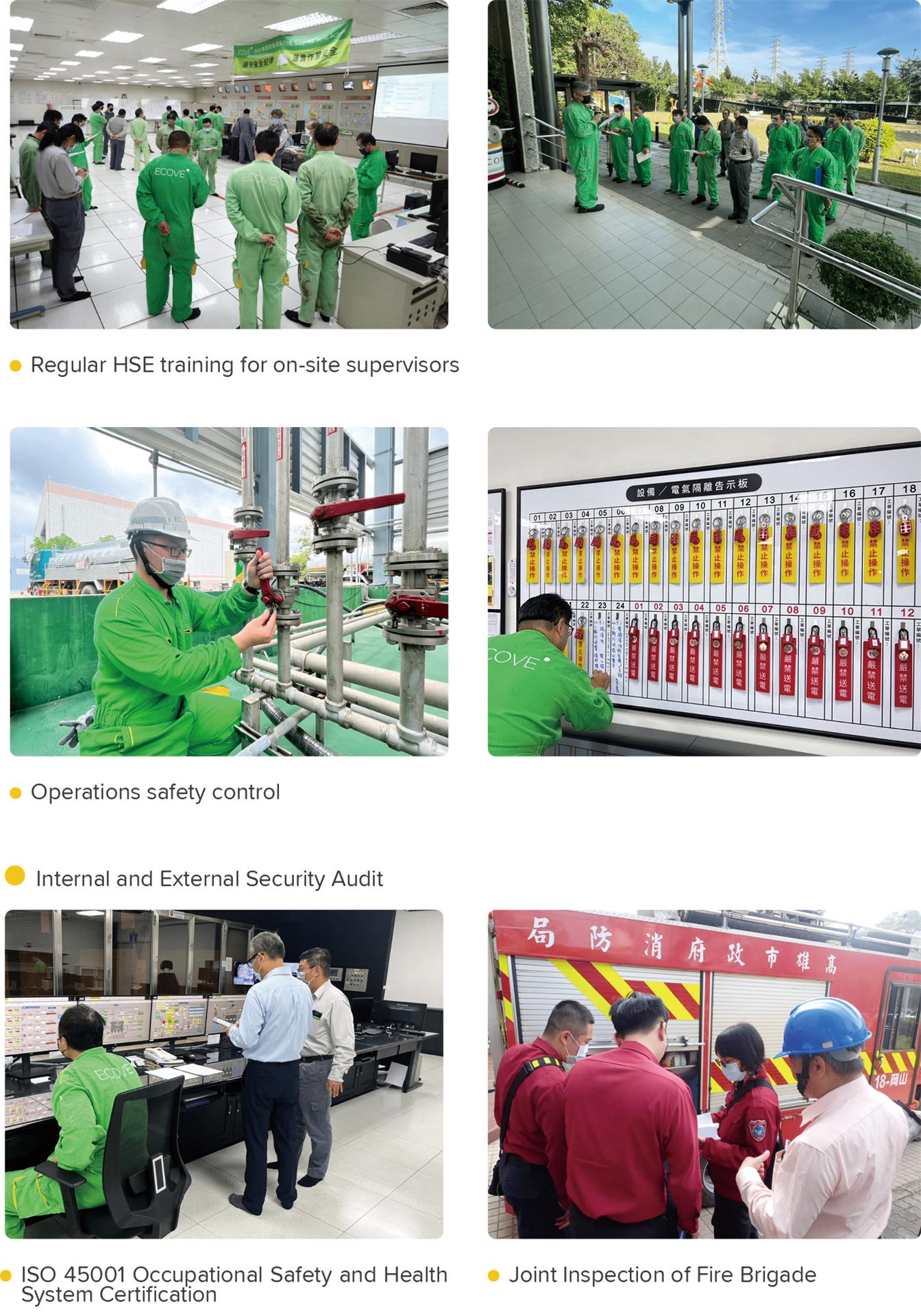

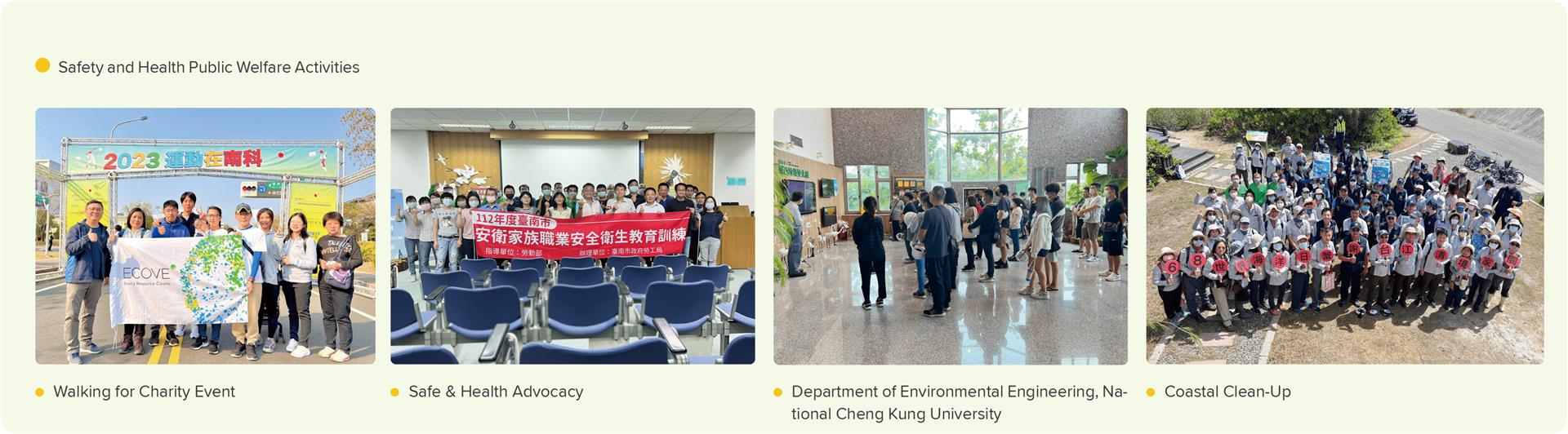